Technological process for continuously producing succinic anhydride and co-producing succinic acid through maleic anhydride hydrogenation
A technology of succinic anhydride and process flow, which is applied in the field of production technology of succinic anhydride/succinic acid, can solve the problems of inability to uniformly remove the reaction heat, reduce the reaction performance of the catalyst, sintering the active components of the catalyst, etc., so as to avoid polymerization accumulation. Carbon or coking, reaction temperature equalization, effect of reducing local hot spot temperature
- Summary
- Abstract
- Description
- Claims
- Application Information
AI Technical Summary
Problems solved by technology
Method used
Image
Examples
Embodiment 1
[0028] 1) The maleic anhydride solution with a concentration of 0.08g / mL (the solvent is a mixture of xylene and cyclohexane) is preheated by the heat exchange device, and then passes through the feed metering device and flows in parallel with hydrogen from the primary hydrogenation reactor 1 The bottom enters the catalyst bed, and the catalyst in the primary hydrogenation reactor is Al 2 o 3 As a supported nickel-based catalyst, the maleic anhydride solution space velocity is 4.2h -1 , the hydrogen pressure is 4MPa, the reaction temperature is 90°C, the maleic anhydride solution overflows to the first gas-liquid separation device 2 after reacting with hydrogen; a part of the hydrogen separated by the first gas-liquid separation device 2 is mixed with fresh hydrogen and re-enters the primary processing The hydrogen reactor 1 is recycled, and the reaction liquid separated by the first gas-liquid separation device 2 is diverted after being deheated by the first heat exchange de...
Embodiment 2
[0032] With the maleic anhydride solution of 0.08g / mL (the solvent is the mixed solution of cyclohexanone and chlorobenzene) as raw material liquid synthetic succinic acid, step is the same as embodiment 1, reaction conditions: primary hydrogenation reactor hydrogen pressure: 6MPa, Hydrogen pressure in the secondary hydrogenation reactor: 4MPa, the catalyst in the primary hydrogenation reactor is SiO 2 -Al 2 o 3 Composite-supported nickel-based catalyst, liquid space velocity: 6h -1 , the catalyst in the secondary hydrogenation reactor is Al 2 o 3Supported nickel-based catalyst as a carrier, liquid space velocity: 1.5h -1 , The reaction temperature of the primary hydrogenation reactor: 150°C, the reaction temperature in the secondary hydrogenation reactor: 80°C, and 1 / 4 of the solution after the reaction in the primary hydrogenation reactor enters the secondary hydrogenation reactor. The reaction results are: the conversion rate of maleic anhydride is between 99.5% and 99...
Embodiment 3
[0034] With the maleic anhydride solution of 0.16g / mL (the solvent is the mixed solution of methyl acetone and ethylene glycol monomethyl ether) as raw material liquid synthetic succinic acid, step is the same as embodiment 1, reaction conditions: primary hydrogenation reactor hydrogenation Pressure: 5MPa, hydrogen pressure in the secondary hydrogenation reactor: 3MPa, the catalyst in the primary hydrogenation reactor is Al 2 o 3 Supported nickel-based catalyst as a carrier, liquid space velocity: 5.6h -1 , the catalyst in the secondary hydrogenation reactor is SiO 2 Supported nickel-based catalyst as a carrier, liquid space velocity: 1.4h -1 , The reaction temperature of the primary hydrogenation reactor: 110°C, the reaction temperature in the secondary hydrogenation reactor: 70°C, 1 / 4 of the solution after the reaction in the primary hydrogenation reactor enters the secondary hydrogenation reactor. The reaction result is: the conversion rate of maleic anhydride is between...
PUM
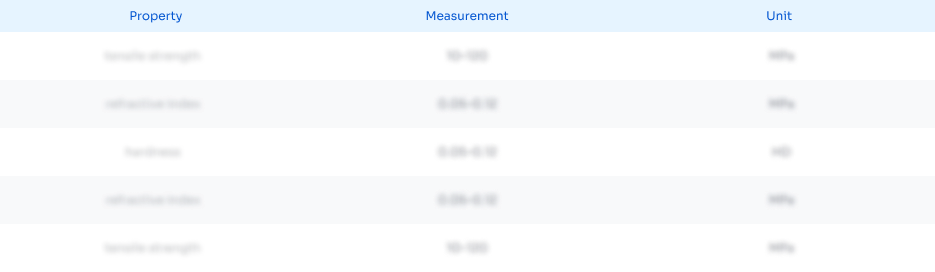
Abstract
Description
Claims
Application Information

- R&D
- Intellectual Property
- Life Sciences
- Materials
- Tech Scout
- Unparalleled Data Quality
- Higher Quality Content
- 60% Fewer Hallucinations
Browse by: Latest US Patents, China's latest patents, Technical Efficacy Thesaurus, Application Domain, Technology Topic, Popular Technical Reports.
© 2025 PatSnap. All rights reserved.Legal|Privacy policy|Modern Slavery Act Transparency Statement|Sitemap|About US| Contact US: help@patsnap.com