Method for converting solid lead chloride into lead oxide
A technology of lead chloride and lead oxide, applied in the direction of lead monoxide and lead oxide, which can solve the problems of chlorine gas escape, environmental pollution, and poor control of the process, so as to avoid escape and leakage, friendly working environment, and process easily controlled effects
- Summary
- Abstract
- Description
- Claims
- Application Information
AI Technical Summary
Problems solved by technology
Method used
Image
Examples
Embodiment 1
[0025] Carry out the first step conversion of solid lead chloride, calcium oxide and water according to a certain liquid-solid ratio. The technical conditions for the first step conversion of lead chloride are: the mass ratio of lead chloride to calcium oxide=9:1, liquid-solid Ratio 4:1, transformation temperature 60°C, reaction time 90 minutes; after the reaction is completed, liquid-solid separation is carried out; the first step conversion slag PbOHCl is carried out in a certain concentration of sodium hydroxide solution for the second step transformation, and after the reaction is completed, liquid Solid separation to obtain conversion slag PbO and secondary conversion liquid. The technical conditions for the second conversion step are: the mass ratio of basic lead chloride to sodium hydroxide=5:1, the concentration of sodium hydroxide solution is 15%, and the conversion reaction The temperature was 75°C, and the reaction time was 75 minutes.
[0026] Results: The conversi...
Embodiment 2
[0030] Carry out the first step conversion of solid lead chloride, calcium oxide and water according to a certain liquid-solid ratio. The technical conditions for the first step conversion of lead chloride are: the mass ratio of lead chloride to calcium oxide=9:1, liquid-solid The ratio is 5:1, the conversion temperature is 70°C, and the reaction time is 120 minutes; after the reaction is completed, the liquid-solid separation is carried out; the first step conversion slag PbOHCl is carried out in a certain concentration of sodium hydroxide solution for the second step conversion, and after the reaction is completed, the liquid Separation of solids to obtain conversion slag PbO and liquid after secondary conversion. The technical conditions for the second step conversion are: the mass ratio of basic lead chloride to sodium hydroxide=4:1, the concentration of sodium hydroxide solution is 15%, and the conversion reaction The temperature was 75°C, and the reaction time was 30 minu...
Embodiment 3
[0035] Carry out the first step conversion of solid lead chloride, calcium oxide and water according to a certain liquid-solid ratio. The technical conditions for the first step conversion of lead chloride are: the mass ratio of lead chloride to calcium oxide=10:1, liquid-solid Ratio 4:1, transformation temperature: 60°C, reaction time 120min; after the reaction is completed, liquid-solid separation is carried out; the first step transformation slag PbOHCl is carried out in a certain concentration of sodium hydroxide solution for the second step transformation, and after the reaction is completed, carry out Liquid-solid separation to obtain conversion slag PbO and liquid after secondary conversion. The technical conditions for the second conversion step are: the mass ratio of basic lead chloride to sodium hydroxide=4.5:1, the concentration of sodium hydroxide solution is 17.5%, and the conversion The reaction temperature was 75°C, and the reaction time was 75 minutes.
[0036]...
PUM
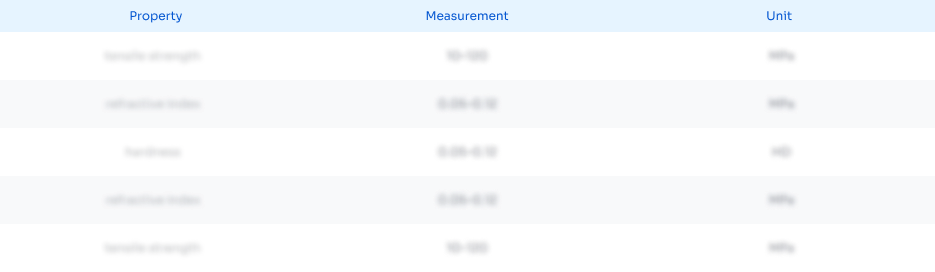
Abstract
Description
Claims
Application Information

- R&D
- Intellectual Property
- Life Sciences
- Materials
- Tech Scout
- Unparalleled Data Quality
- Higher Quality Content
- 60% Fewer Hallucinations
Browse by: Latest US Patents, China's latest patents, Technical Efficacy Thesaurus, Application Domain, Technology Topic, Popular Technical Reports.
© 2025 PatSnap. All rights reserved.Legal|Privacy policy|Modern Slavery Act Transparency Statement|Sitemap|About US| Contact US: help@patsnap.com