A biomass combustion utilization method for docking boilers and heat exchangers
A heat exchanger and biomass fuel technology, applied in the field of combustion, can solve the problems of easy blockage of pipelines, easy coking, and easy coking of biomass burners, so as to ensure continuous and stable operation, reduce the number of shutdowns for slag cleaning, Increase the fire temperature and the effect of
- Summary
- Abstract
- Description
- Claims
- Application Information
AI Technical Summary
Problems solved by technology
Method used
Image
Examples
Embodiment 1
[0041] A biomass combustion utilization method for docking boilers and heat exchangers in this embodiment includes the following steps:
[0042] (1) Preliminary pyrolysis: Preliminary pyrolysis of biomass raw materials at a pyrolysis temperature of 260-420°C to precipitate tar and obtain biomass fuel;
[0043] Preliminary pyrolysis of biomass raw materials is carried out at a temperature of 260~420°C to effectively precipitate tar and obtain biomass fuel with low tar content. Since the tar content of the biomass fuel after preliminary pyrolysis is low, close to zero, it avoids coking during combustion. If the situation occurs, it can prevent the coked carbon deposit from adhering to the water wall, blocking the sieve plate and pipes and other components, ensuring the continuous and stable operation of the biomass burner, effectively reducing the number of shutdowns to clean the slag, improving the working efficiency of the biomass burner and extending the operating life of the ...
Embodiment 2
[0051] A biomass combustion utilization method for docking boilers and heat exchangers in this embodiment includes the following steps:
[0052] (1) Preliminary cracking: put the biomass raw material in the cracking device for preliminary cracking, such as figure 1 As shown, the cracking device includes a driving device 1, a screw 4 and a barrel 3, the driving device 1 is connected to the screw 4, the screw 4 is rotatably inserted inside the barrel 3, and the inner wall of the barrel 3 is provided with a heating layer and Insulation layer, the insulation layer is set between the inner wall of the barrel 3 and the heating layer, and a cracking zone is formed between the screw 4 and the heating layer; the temperature in the cracking zone is 260~420°C, the outlet temperature is 200~250°C, and the cracking time is After 20-50 minutes, the biomass raw material is initially cracked in the cracking zone and tar is precipitated to obtain biomass fuel. The cracked gas and tar are disch...
Embodiment 3
[0068] The difference between the biomass combustion utilization method for docking boilers and heat exchangers in this embodiment and embodiment 2 is that
[0069] (1) In the initial cracking, the cracking temperature is 260°C, and the outlet temperature is 200-250°C. At this cracking temperature, tar can be precipitated and the calorific value of biomass fuel can be retained. The cracking time is 40 minutes.
[0070] (2) During feed combustion, the ventilation volume of 1kg biomass fuel is 4.5Nm 3 , proper ventilation, good combustion effect.
[0071] The main technical solutions of this embodiment are basically the same as those of Embodiment 1 or Embodiment 2, and the features not explained in this embodiment are explained in Embodiment 1 or Embodiment 2, and will not be repeated here.
PUM
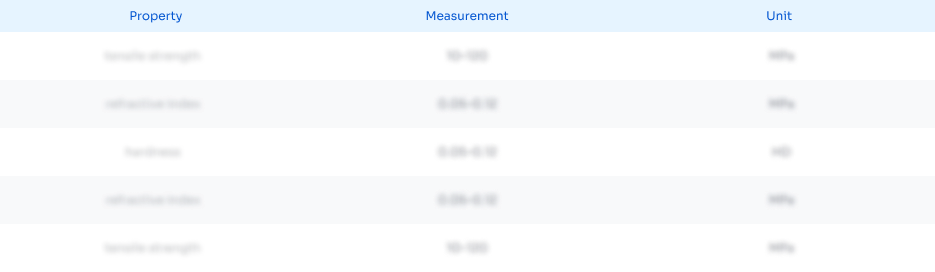
Abstract
Description
Claims
Application Information

- R&D
- Intellectual Property
- Life Sciences
- Materials
- Tech Scout
- Unparalleled Data Quality
- Higher Quality Content
- 60% Fewer Hallucinations
Browse by: Latest US Patents, China's latest patents, Technical Efficacy Thesaurus, Application Domain, Technology Topic, Popular Technical Reports.
© 2025 PatSnap. All rights reserved.Legal|Privacy policy|Modern Slavery Act Transparency Statement|Sitemap|About US| Contact US: help@patsnap.com