Casting steel for railway vehicle bolster side frame and preparation method thereof
A technology for railway vehicles and castings is applied in the field of casting steel for bolster side frames of railway vehicles and its preparation, which can solve the problems of metallographic structure influence of castings, long heat treatment time, influence on grain size of bolster side frames, etc. The effect of grain boundary weakening
- Summary
- Abstract
- Description
- Claims
- Application Information
AI Technical Summary
Problems solved by technology
Method used
Image
Examples
Embodiment Construction
[0026] In order to better explain the present invention, the main content of the present invention is further clarified below in conjunction with specific examples, but the content of the present invention is not limited to the following examples.
[0027] A casting steel for preparing bolster side frames, the chemical composition of the casting steel is: C: 0.23-0.29%, Si: 0.30-0.50%, Mn: 0.80-1.00%, P≤0.030%, S ≤0.030%, Cu≤0.30%, Ni: 0.20~0.50%, Cr: 0.30~0.40%, Al: 0.020~0.050%, rare earth ≤0.10%, the balance is Fe, wherein, La≤30% in the rare earth , Ce≤70%.
[0028] A method for preparing cast steel, comprising the steps of:
[0029] 1) Weigh according to the above weight percentage: C, Si, Mn, P, S, Cu, Ni, Cr, Al, rare earth corresponding raw materials, set aside;
[0030] 2) Put the raw materials corresponding to C, P, S, Cu and Ni into the eccentric bottom electric arc furnace to melt into molten steel, add 7-9kg of recarburizer per ton of molten steel, and control t...
PUM
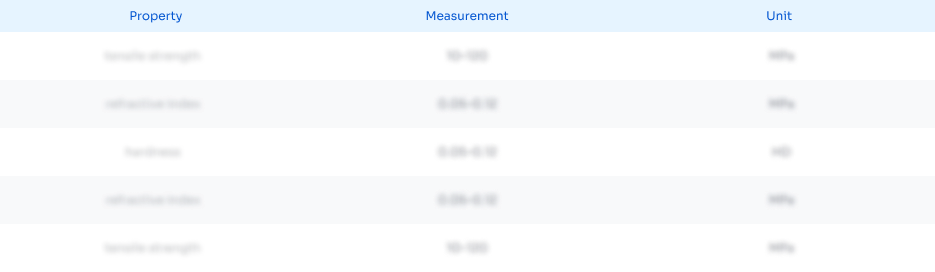
Abstract
Description
Claims
Application Information

- R&D
- Intellectual Property
- Life Sciences
- Materials
- Tech Scout
- Unparalleled Data Quality
- Higher Quality Content
- 60% Fewer Hallucinations
Browse by: Latest US Patents, China's latest patents, Technical Efficacy Thesaurus, Application Domain, Technology Topic, Popular Technical Reports.
© 2025 PatSnap. All rights reserved.Legal|Privacy policy|Modern Slavery Act Transparency Statement|Sitemap|About US| Contact US: help@patsnap.com