Preparation method of wood fiber biomass film
A technology of lignocellulosic and biomass, which is applied in the field of biomass refining, can solve the problems of insoluble and low utilization efficiency of lignocellulosic biomass, and achieve the effects of strong dissolving ability, good ultraviolet absorption function and simple process
- Summary
- Abstract
- Description
- Claims
- Application Information
AI Technical Summary
Problems solved by technology
Method used
Image
Examples
Embodiment 1
[0021] Embodiment 1: Lignocellulosic biomass adopts bagasse
[0022] A preparation method of lignocellulosic biomass film, comprising the steps of:
[0023] Step 1. pulverize the dried bagasse, and collect the 160 mesh sieve part;
[0024] Step 2. Take 0.5g of crushed bagasse powder and disperse it in 10g of DMSO / LiCl (the mass percentage of LiCl is 10%), and stir for 10h at 90°C under nitrogen protection to completely dissolve the bagasse to obtain a film liquid;
[0025] Step 3. Pour the film-making solution obtained in step 2 onto a glass plate, scrape it flat with a scraper, soak it in an acetone / water mixed solution (where the volume ratio of acetone to water is 9:1) to remove the solvent, and dry to obtain regeneration Bagasse film.
[0026] According to GB / T1040.3-2006, the prepared bagasse film was tested for tensile properties using a universal tensile machine. The obtained film can withstand a maximum stress of 30.8MPa, a Young's modulus of 1.43GPa, and a breaking...
Embodiment 2
[0029] Example 2: lignocellulosic biomass using corn stalks
[0030] A preparation method of lignocellulosic biomass film, comprising the steps of:
[0031] Step 1. Pulverize the dried corn stalks and collect the part through a 160-mesh sieve;
[0032] Step 2. Disperse 0.5 g of crushed corn stalk powder in 50 g of DMSO / LiCl (LiCl mass percentage 6%), and stir for 24 hours at 20°C under nitrogen protection to completely dissolve the corn stalk to obtain a film-making solution ;
[0033] Step 3. Pour the film-making solution obtained in step 2 onto a glass plate, scrape it flat with a scraper, soak in ethanol to remove the solvent, and dry to obtain a regenerated cornstalk film.
[0034] The prepared cornstalk film was tested according to GB / T1040.3-2006 using a universal tensile machine. The obtained film can withstand a maximum stress of 7.92MPa, a Young's modulus of 486MPa, and an elongation at break of 2.44%. .
[0035] The UV-Vis absorption spectra of the prepared films...
Embodiment 3
[0036] Embodiment 3: lignocellulosic biomass adopts masson pine
[0037] A preparation method of lignocellulosic biomass film, comprising the steps of:
[0038] Step 1. pulverize the dried Pinus massoniana, and collect the 160 mesh sieve part;
[0039] Step 2. Place 0.5 g of pulverized pine masson powder in 2.5 g of DMSO / LiCl (LiCl mass percentage content 2%), stir for 2 hours at 130 ° C under nitrogen protection conditions, completely dissolve the masson pine powder, and obtain the prepared Membrane fluid;
[0040] Step 3. Pour the film-making solution obtained in step 2 onto a glass plate, scrape it flat with a scraper, soak in isopropanol to remove the solvent, and dry to obtain a regenerated masson pine film.
[0041] The prepared masson pine film was tested according to GB / T1040.3-2006 using a universal tensile machine. The obtained film can withstand a maximum stress of 52.6MPa, a Young's modulus of 2.65GPa, and an elongation at break of 3.90 %.
[0042] The UV-Vis a...
PUM
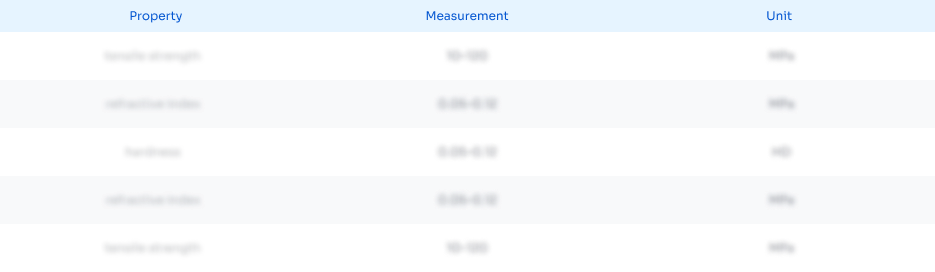
Abstract
Description
Claims
Application Information

- R&D
- Intellectual Property
- Life Sciences
- Materials
- Tech Scout
- Unparalleled Data Quality
- Higher Quality Content
- 60% Fewer Hallucinations
Browse by: Latest US Patents, China's latest patents, Technical Efficacy Thesaurus, Application Domain, Technology Topic, Popular Technical Reports.
© 2025 PatSnap. All rights reserved.Legal|Privacy policy|Modern Slavery Act Transparency Statement|Sitemap|About US| Contact US: help@patsnap.com