Technology for preparing ammonium sulfate by high-efficiency ammonia desulphurization and crystallization
A technology of ammonia desulfurization and ammonium sulfate, which is applied in the field of flue gas desulfurization and dust removal, can solve the problems of unfavorable safety production, increased operating costs, and high liquid level in the oxidation tank, so as to reduce equipment investment and production energy consumption, improve production efficiency, and obtain high rate effect
- Summary
- Abstract
- Description
- Claims
- Application Information
AI Technical Summary
Problems solved by technology
Method used
Examples
Embodiment 1
[0030] A. Desulfurization: The flue gas to be desulfurized and the atomized ammonia water are passed into the desulfurization section of the desulfurization tower at a volume ratio of 400:1, and the slurry containing ammonium bisulfite and ammonium sulfite generated after the reaction desulfurization enters the regeneration storage tank.
[0031] B. Oxidation: Pass ammonia water into the regeneration storage tank, control the pH value of the slurry in the regeneration storage tank to 6.0, after the ammonia water and ammonium bisulfite react to form ammonium sulfite, then pass the atomized ammonium sulfite solution into the In the oxidation section of the desulfurization tower, the volume ratio of the atomized ammonium sulfite solution to the oxygen-enriched flue gas is 1:400, and the oxidation takes 150 minutes. The slurry containing ammonium sulfate produced by the reaction of ammonium sulfite and oxygen-enriched flue gas enters the concentration storage tank.
[0032] C. Con...
Embodiment 2
[0034] A. Desulfurization: The flue gas to be desulfurized and the atomized ammonia water are passed into the desulfurization section of the desulfurization tower at a volume ratio of 380:1, and the slurry containing ammonium bisulfite and ammonium sulfite generated after the reaction desulfurization enters the regeneration storage tank.
[0035] B. Oxidation: Pass ammonia water into the regeneration storage tank, control the pH value of the slurry in the regeneration storage tank to 6.5, after the ammonia water and ammonium bisulfite react to form ammonium sulfite, then pass the atomized ammonium sulfite solution into the In the oxidation section of the desulfurization tower, the volume ratio of the atomized ammonium sulfite solution to the oxygen-enriched flue gas is 1:380, and the oxidation takes 120 minutes. The slurry containing ammonium sulfate produced by the reaction of ammonium sulfite and oxygen-enriched flue gas enters the concentration storage tank.
[0036] C. Con...
Embodiment 3
[0038] A. Desulfurization: The flue gas to be desulfurized and the atomized ammonia water are passed into the desulfurization section of the desulfurization tower at a volume ratio of 420:1, and the slurry containing ammonium bisulfite and ammonium sulfite generated after the reaction desulfurization enters the regeneration storage tank.
[0039] B. Oxidation: Pass ammonia water into the regeneration storage tank, control the pH value of the slurry in the regeneration storage tank to 5.5, after the ammonia water and ammonium bisulfite react to generate ammonium sulfite, then pass the atomized ammonium sulfite solution into the In the oxidation section of the desulfurization tower, the volume ratio of the atomized ammonium sulfite solution to the oxygen-enriched flue gas is 1:420, and the oxidation is 180 minutes. The slurry containing ammonium sulfate produced by the reaction of ammonium sulfite and oxygen-enriched flue gas enters the concentration storage tank.
[0040] C. Co...
PUM
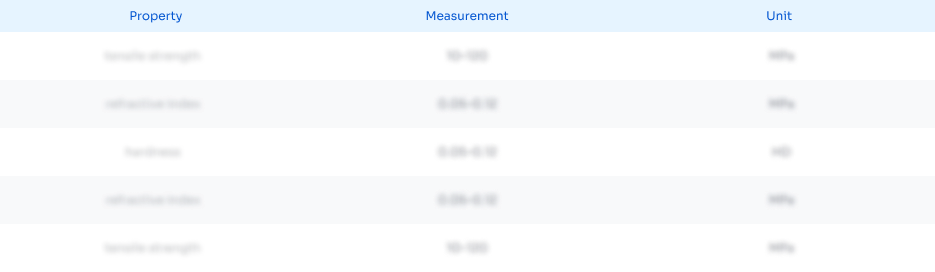
Abstract
Description
Claims
Application Information

- R&D
- Intellectual Property
- Life Sciences
- Materials
- Tech Scout
- Unparalleled Data Quality
- Higher Quality Content
- 60% Fewer Hallucinations
Browse by: Latest US Patents, China's latest patents, Technical Efficacy Thesaurus, Application Domain, Technology Topic, Popular Technical Reports.
© 2025 PatSnap. All rights reserved.Legal|Privacy policy|Modern Slavery Act Transparency Statement|Sitemap|About US| Contact US: help@patsnap.com