Rail vehicle blank structure and its manufacturing method
A rail vehicle and blank technology, which is applied in the direction of railway car bodies, railway car body parts, railway roofs, etc., can solve problems such as unfavorable surfaces, achieve stress-free warping, avoid material doubling, and reduce weight
- Summary
- Abstract
- Description
- Claims
- Application Information
AI Technical Summary
Problems solved by technology
Method used
Image
Examples
Embodiment Construction
[0082] exist figure 1 An outer wall module 1 is schematically shown in . The outer wall module comprises an outer sheet metal structure 3 which is closed at the upper end by a horizontally extending upper flange profile 2 . The outer sheet metal structure 3 of the outer wall module 1 is made of sheet metal, including at least a first sheet metal 10 and a second sheet metal 11 with different strength properties, together with the upper flange profile 2 . exist figure 1 The inner side 17 of the outer sheet metal structure is shown in , to which the frame 4 made of frame profiles 5 is fastened. The outer sheet metal structure 3 forms a smooth outer surface on the outer side 18 (below the plane of the drawing), in which functional openings or cutouts in the form of windows 7 are formed. In the embodiment shown, the first metal sheet 10 and the second metal sheet 11 have different material thicknesses. The outer sheet metal structure 3 with the upper flange profile 2 is configu...
PUM
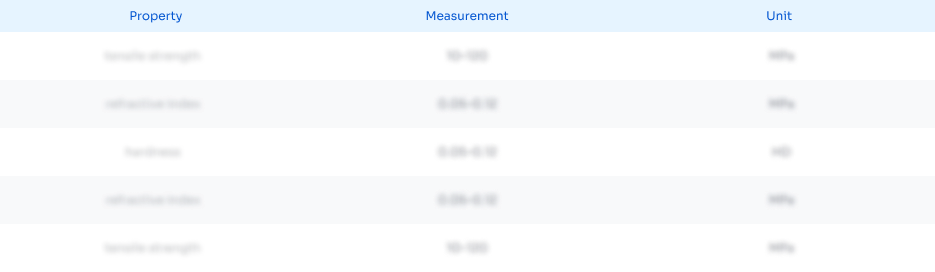
Abstract
Description
Claims
Application Information

- R&D Engineer
- R&D Manager
- IP Professional
- Industry Leading Data Capabilities
- Powerful AI technology
- Patent DNA Extraction
Browse by: Latest US Patents, China's latest patents, Technical Efficacy Thesaurus, Application Domain, Technology Topic, Popular Technical Reports.
© 2024 PatSnap. All rights reserved.Legal|Privacy policy|Modern Slavery Act Transparency Statement|Sitemap|About US| Contact US: help@patsnap.com