Novel bearing zinc alloy
A zinc alloy and bearing technology, applied in the field of zinc alloys for new bearings, can solve the problems of low service temperature, affecting the application of zinc-based alloys, and a wide range of alloy solidification temperature, and achieve improved performance, excellent die casting and aging performance, excellent The effect of normal temperature mechanical properties
- Summary
- Abstract
- Description
- Claims
- Application Information
AI Technical Summary
Problems solved by technology
Method used
Image
Examples
Embodiment 1-4, and comparative example 1-9
[0019] 1) Ingredients: According to the alloy ratio given in Table 1, the alloy ingredients come from pure zinc with a purity of 99.99%, aluminum-silicon alloy with a weight ratio of 1:1, zinc-antimony alloy with a weight ratio of 1:1, Aluminum scandium alloy, electrolytic copper, industrial pure magnesium, pure aluminum and other raw materials with a weight ratio of 1:1.
[0020] 2) Melting: first place pure zinc in a smelting furnace and heat up to 460°C for 10 minutes, then raise the temperature to 830°C and add industrial pure aluminum, aluminum-silicon alloy, aluminum-scandium alloy and electrolytic copper and continue stirring until the aluminum-silicon alloy and electrolytic copper are completely melted, then lower the temperature to 690°C and add zinc-antimony alloy and continue to stir until the zinc-antimony alloy is completely melted, then lower the temperature to 640°C and press industrial pure magnesium to the bottom of the melt for at least 5 minutes, then stir th...
Embodiment 5-7
[0032] In Examples 5-7, and Comparative Examples 10-17, the chemical composition of the alloy is the same as in Example 2, and the optimization of process parameters in the die-casting process is mainly investigated. The selection of parameters and performance results are shown in Table 2.
[0033] Although it is a well-known technology in the art to use two different melt flow rates of low speed and high speed to control defects such as pores in the die-casting process, it can be seen from the results in Table 2 that how to choose the melt flow rate and casting pressure still has a great influence :
[0034] For the melt flow rate and casting pressure of the zinc alloy of the present invention at the low-speed stage, the melt flow rate should be controlled between 0.5-0.8m / s. Too low melt flow rate will cause the melt to cool down too fast and affect the die-casting of the melt performance, which eventually deteriorates the mechanical properties of the alloy, and is also not ...
Embodiment 8-9
[0040] In Examples 8-9, and Comparative Examples 18-21, the chemical composition of the alloy is the same as in Example 2, and the optimization of heat treatment process parameters is mainly investigated. The selection of parameters and performance results are shown in Table 3.
[0041] table 3
[0042]
[0043]
[0044] It can be seen from the results in Table 3 that the homogenization temperature should not be too low, and it needs enough time, otherwise it will be difficult to eliminate stress and improve the mechanical properties; on the contrary, if the temperature is too high, it may cause changes in the structure and seriously affect the mechanical properties. . The aging temperature must also be appropriate. Too low aging temperature and time cannot play a role in obtaining stable mechanical properties, while too high aging temperature will seriously affect the strength of the alloy.
[0045] To sum up, the present invention first rationally designs the compositio...
PUM
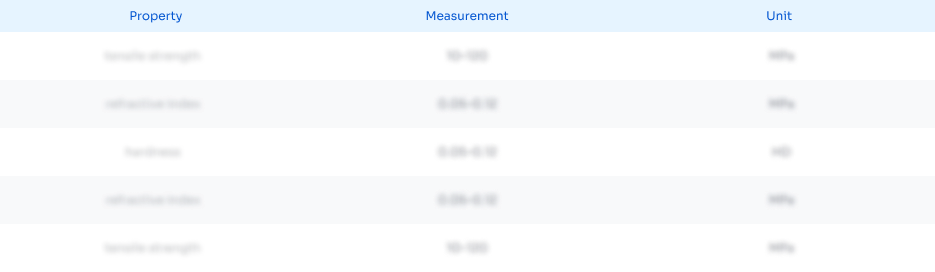
Abstract
Description
Claims
Application Information

- R&D
- Intellectual Property
- Life Sciences
- Materials
- Tech Scout
- Unparalleled Data Quality
- Higher Quality Content
- 60% Fewer Hallucinations
Browse by: Latest US Patents, China's latest patents, Technical Efficacy Thesaurus, Application Domain, Technology Topic, Popular Technical Reports.
© 2025 PatSnap. All rights reserved.Legal|Privacy policy|Modern Slavery Act Transparency Statement|Sitemap|About US| Contact US: help@patsnap.com