Styrene-ethylene-butadiene-styrene (SEBS) thermoplastic elastomer bra lining material as well as preparation method and application thereof
A thermoplastic elastomer and cushion material technology, applied in bras, applications, clothing, etc., can solve the problems of anti-oxidation, poor anti-allergic, easy to cause allergic reactions, easy to age, etc., and achieve economic and social benefits that are not easily soaked in water Significant, easy-to-operate effects
- Summary
- Abstract
- Description
- Claims
- Application Information
AI Technical Summary
Problems solved by technology
Method used
Image
Examples
Embodiment 1
[0021] 1) Mixing material: According to the ratio of parts by mass, add 100 parts of powdery high molecular weight (about 220,000) SEBS elastomer into a high-speed mixer and stir for 5 minutes, then add 400 parts of naphthenic rubber oil, and stir for another 20 minutes , to obtain oil-extended SEBS elastomer. Add 0.5 parts of alkyl polyphenol antioxidant 1010, 0.5 part of phosphite antioxidant 168, 1 part of polyethylene wax, and 50 parts of talc powder (1250 mesh) to the oil-extended SEBS elastomer, at high speed Blend for 15 minutes;
[0022] 2) Pelletizing: Put the uniformly mixed material into a twin-screw extruder to extrude and granulate. The process conditions for granulation are 150-155°C in the feeding section, 165-170°C in the melting and compression section, and 165-170°C in the homogenizing section. 170-175°C, the die temperature is 170°C, the screw speed is 250-350 rpm;
[0023] 3) Injection: Add the prepared pellets to the injection machine for injection moldi...
Embodiment 2
[0027] 1) Mixing material: Add 100 parts of powdered low molecular weight (about 70,000) SEBS elastomer into a high-speed mixer and stir for 5 minutes, then add 100 parts of naphthenic rubber oil and 100 parts of paraffin base rubber oil, and then stirred for 20 minutes to obtain an oil-extended SEBS elastomer. 15 parts of EVA resin, 0.5 part of maleic anhydride grafted SEBS, 0.5 part of alkyl polyphenol antioxidant 1010, 0.5 part of alkyl polyphenol antioxidant DLTP, 1 part of zinc stearate, 35 parts of talcum powder (1250 mesh) added to the oil-extended SEBS elastomer, and stirred for 15 minutes in a high-speed mixer;
[0028] 2) Pelletizing: Put the uniformly mixed material into a twin-screw extruder to extrude and granulate. The process conditions for granulation are 150-155°C in the feeding section, 170-175°C in the melting and compression section, and 170-175°C in the homogenizing section. 175-180°C, the die temperature is 175°C, the screw speed is 250-350 rpm;
[0029...
Embodiment 3
[0031] 1) Mixing material: Add 50 parts of powdery high molecular weight (about 220,000) SEBS elastomer and 50 parts of low molecular weight (about 70,000) SEBS elastomer into a high-speed mixer and stir for 5 minutes before adding 250 parts of paraffin-based rubber oil were stirred for another 20 minutes to obtain an oil-extended SEBS elastomer. Add 0.5 part of alkyl polyphenol antioxidant 1010, 0.5 part of antioxidant phosphite 168, 0.5 part of colorant, 1 part of calcium stearate, 30 parts of light calcium carbonate (800 mesh) to the oil-extended Type SEBS elastomer, stir for 15 minutes in a high-speed mixer;
[0032] 2) Pelletizing: Put the uniformly mixed material into a twin-screw extruder to extrude and granulate. The process conditions for granulation are 150-155°C in the feeding section, 165-170°C in the melting and compression section, and 165-170°C in the homogenizing section. 170-175°C, the die temperature is 170°C, the screw speed is 250-350 rpm;
[0033] 3) Inj...
PUM
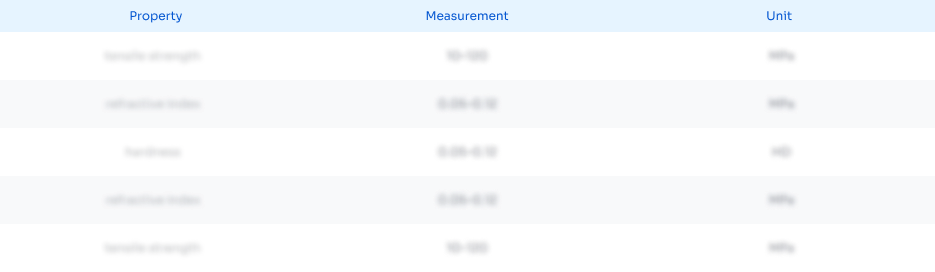
Abstract
Description
Claims
Application Information

- R&D
- Intellectual Property
- Life Sciences
- Materials
- Tech Scout
- Unparalleled Data Quality
- Higher Quality Content
- 60% Fewer Hallucinations
Browse by: Latest US Patents, China's latest patents, Technical Efficacy Thesaurus, Application Domain, Technology Topic, Popular Technical Reports.
© 2025 PatSnap. All rights reserved.Legal|Privacy policy|Modern Slavery Act Transparency Statement|Sitemap|About US| Contact US: help@patsnap.com