A test method for a camera shutter micro-vibration physical simulation test processing system
A camera shutter and processing system technology, applied in optics, instruments, photography, etc., can solve the problems of model establishment, calibration and inspection with considerable difficulty, and achieve the effects of improving measurement accuracy, improving adaptability, and improving reliability.
- Summary
- Abstract
- Description
- Claims
- Application Information
AI Technical Summary
Problems solved by technology
Method used
Image
Examples
Embodiment Construction
[0027] Such as figure 1 As shown, a camera shutter micro-vibration physical simulation test processing system includes a camera shutter 3, an acceleration sensor 4, a hexagonal adapter plate 2, a six-component eight-sensor vibration force test bench 1, and a data acquisition and processing system 5; The six-component eight-sensor disturbance force test bench 1 is connected to the camera shutter 3 through the hexagonal adapter plate 2; the external controller is connected to the camera shutter 3 to control the switch of the camera shutter 3; the data acquisition and processing system 5 and the six The component eight-sensor vibration disturbance test bench 1 is connected; the six-component eight-sensor vibration disturbance test bench 1 measures the micro-vibration data of the camera shutter 3 during operation, and sends it to the data acquisition and processing system 5 for analysis and processing, and obtains the camera shutter 3 of the disturbing force.
[0028] The data ac...
PUM
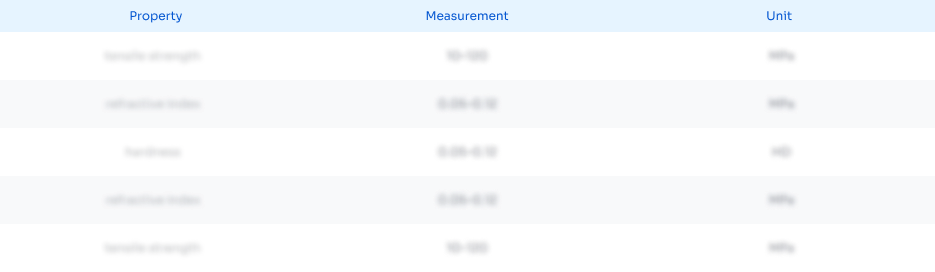
Abstract
Description
Claims
Application Information

- Generate Ideas
- Intellectual Property
- Life Sciences
- Materials
- Tech Scout
- Unparalleled Data Quality
- Higher Quality Content
- 60% Fewer Hallucinations
Browse by: Latest US Patents, China's latest patents, Technical Efficacy Thesaurus, Application Domain, Technology Topic, Popular Technical Reports.
© 2025 PatSnap. All rights reserved.Legal|Privacy policy|Modern Slavery Act Transparency Statement|Sitemap|About US| Contact US: help@patsnap.com