Thin type micro villus polyurethane certificate leather and preparation method thereof
A polyurethane, fleece-thin technology, used in textiles and papermaking, roughening, fabric surface trimming, etc., can solve the problems of easy color fading, fineness of fleece effect, poor air and moisture permeability, etc., to improve color fastness, color Brilliant, durability-enhancing effects
- Summary
- Abstract
- Description
- Claims
- Application Information
AI Technical Summary
Problems solved by technology
Method used
Examples
Embodiment 1
[0028] 1. Preparation of polyurethane slurry
[0029] Prepared with wet synthetic leather production equipment, add 220 parts of solvent N,N'-dimethylformamide DMF, 0.3 part of color dispersant BYK-104, 0.3 part of penetrant BYK-6798, JRS wood 8 parts of plain powder and 15 parts of color paste BLPN-560, stirred for 30-60 minutes at normal temperature and pressure, then added 100 parts of polyester polyurethane resin HDW-3050, continued stirring for 30-50 minutes at normal temperature and pressure, and then Stirring for 30-60 minutes under the condition of ≤-0.75 bar to obtain polyurethane slurry.
[0030] Among them, the color dispersant BYK-104 and the penetrant BYK-6798 are products of BYK Chemical Company of Germany; the lignin is the product of JRS Company of Germany; the color paste BLPN-560 is the product of Zhejiang Shenlan Chemical Co., Ltd.; the polyester polyurethane resin HDW -3050 is a product of Jiangsu Huada New Material Co., Ltd.
[0031] The polyurethane slu...
Embodiment 2
[0053] Adopt the same process as in Example 1, but step 1) In the preparation of polyurethane slurry, the raw material ratio is: 230 parts of N,N'-dimethylformamide DMF, 0.2 part of color dispersant BYK-104, penetrant BYK- 0.5 parts of 6798, 6 parts of JRS lignin, 13 parts of color paste BLPN-560, 120 parts of polyester polyurethane resin HDW-3050;
[0054] Step 4) In the post-processing color change, the raw material ratio of the color change paste is: 80 parts by mass of polyurethane color change paste UA-135G, 10 parts by mass of butanone, and 3 parts by mass of ink BLPP-509. Others are the same as embodiment 1.
[0055] The micro-velvet thin document leather prepared by the above method presents a delicate fluffy appearance, soft hand feeling, light weight, similar to genuine leather, and the thickness is equivalent to cloth base. After directional polishing, in addition to soft hand feeling, it also has It improves the air permeability of the leather, improves the color ...
Embodiment 3
[0057] Adopt the same process as in Example 1, but step 1) In the preparation of polyurethane slurry, the raw material ratio is: 260 parts of N,N'-dimethylformamide DMF, 0.6 part of color dispersant BYK-104, penetrant BYK- 6798 0.1 parts, JRS lignin 20 parts, color paste BLPN-560 13 parts, polyester polyurethane resin HDW-3050 120 parts;
[0058] Step 4) In the post-processing color change, the raw material ratio of the color change paste is: 45 parts by mass of polyurethane color change paste UA-135G, 5 parts by mass of butanone, and 1 part by mass of ink BLPP-509. Others are the same as embodiment 1.
[0059] The micro-velvet thin document leather prepared by the above method presents a delicate fluffy appearance, soft hand feeling, light weight, similar to genuine leather, and the thickness is equivalent to cloth base. After directional polishing, in addition to soft hand feeling, it also has It improves the air permeability of the leather, improves the color fastness and ...
PUM
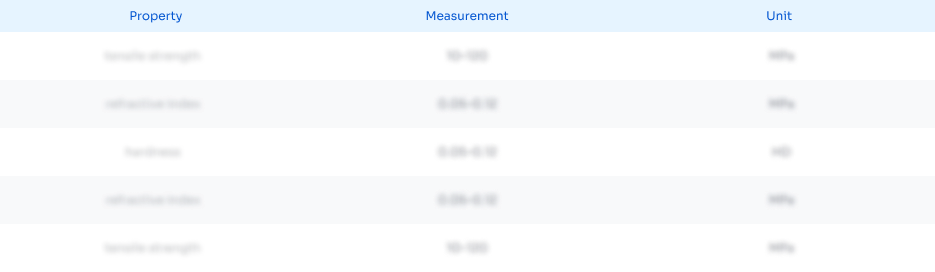
Abstract
Description
Claims
Application Information

- R&D
- Intellectual Property
- Life Sciences
- Materials
- Tech Scout
- Unparalleled Data Quality
- Higher Quality Content
- 60% Fewer Hallucinations
Browse by: Latest US Patents, China's latest patents, Technical Efficacy Thesaurus, Application Domain, Technology Topic, Popular Technical Reports.
© 2025 PatSnap. All rights reserved.Legal|Privacy policy|Modern Slavery Act Transparency Statement|Sitemap|About US| Contact US: help@patsnap.com