Preset control method for thickness flying gauge change of hot-dip zinc coating
A technology that dynamically changes specifications and coating thickness, and is used in hot-dip plating processes, coatings, metal material coating processes, etc.
- Summary
- Abstract
- Description
- Claims
- Application Information
AI Technical Summary
Problems solved by technology
Method used
Image
Examples
Embodiment Construction
[0074] Taking a cold rolling mill No. 5 hot-dip galvanizing line as an example, the present invention will be described in detail.
[0075] The target plating thickness of the system is divided into six specifications, namely 80g / m 2 , 100g / m 2 , 120g / m 2 , 180g / m 2 , 220g / m 2 ,276g / m 2 , The strip speed is 60-130m / min, the distance between the coating thickness gauge and the air knife is 140m, the lag time is 80-300s, the sampling time T=10ms, the time constant T c =8-30s, the plate thickness is 0.4-3.0mm, the transition time when the strip steel specification is changed is 50s. The system preset model adaptive control function consists of: figure 1 Shown. The preset model output variables are air knife distance and air knife pressure. The realization process of parameter adaptive adjustment, such as figure 2 Shown. It is mainly composed of data acquisition and stability analysis unit, coating thickness setting model unit, model long-term preset control unit, model short-term...
PUM
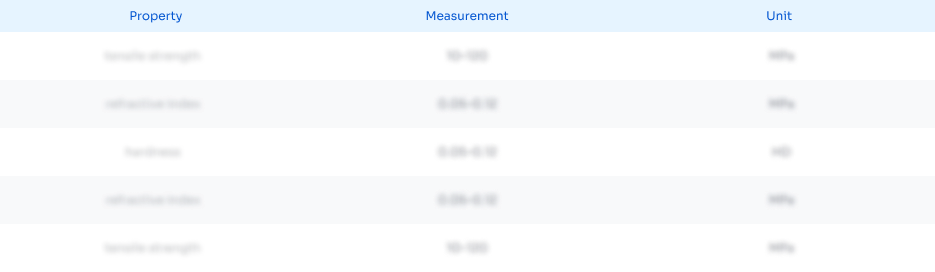
Abstract
Description
Claims
Application Information

- R&D
- Intellectual Property
- Life Sciences
- Materials
- Tech Scout
- Unparalleled Data Quality
- Higher Quality Content
- 60% Fewer Hallucinations
Browse by: Latest US Patents, China's latest patents, Technical Efficacy Thesaurus, Application Domain, Technology Topic, Popular Technical Reports.
© 2025 PatSnap. All rights reserved.Legal|Privacy policy|Modern Slavery Act Transparency Statement|Sitemap|About US| Contact US: help@patsnap.com