Method for measuring thickness of coating in confocal mode
A layer thickness, confocal technology, applied in the detection field, can solve problems such as changes, edge bulges, and cone wear, and achieve the effect of improving measurement accuracy and work efficiency
- Summary
- Abstract
- Description
- Claims
- Application Information
AI Technical Summary
Problems solved by technology
Method used
Image
Examples
Embodiment 1
[0039] The color-coated steel plate is used, and the thickness of the color-coated topcoat is measured by combining V-shaped drilling and laser confocal technology.
[0040] 1) Use a conical head with a taper of 30° to drill a V-shaped hole on the surface of the color-coated steel plate with a depth of 0.15mm. See figure 1
[0041] 2) Focus on the V-shaped hole area in the visible light mode of the laser confocal microscope, and enter the laser mode after it is clear.
[0042] 3) Scan layer by layer in laser mode to obtain the two-dimensional shape of the V-shaped hole.
[0043] 4) Perform noise and filter processing on the two-dimensional topography map, and switch to three-dimensional topography, such as figure 2 shown.
[0044] 5) Select figure 2 The measurement point 1 of the junction between the medium color coating and the substrate and the measurement point 2 that is 2.5 times away from the edge of the V-shaped hole, read the height difference between point 1 an...
Embodiment 2
[0046] Using hot-dip galvanized steel plate, the thickness of galvanized layer is measured by combining V-shaped drilling and laser confocal technology.
[0047] 1) Use a conical head with a taper of 20° to drill a V-shaped hole on the surface of the color-coated steel plate, and the hole depth is about 0.15mm.
[0048] 2) Use 0.5vol% nital to etch the V-shaped hole area so that the zinc layer and the substrate can be distinguished in confocal mode.
[0049] 2) Focus on the V-shaped hole area in the visible light mode of the laser confocal microscope, and enter the laser mode after it is clear.
[0050] 3) Scan layer by layer in laser mode to obtain the two-dimensional shape of the V-shaped hole.
[0051] 4) Perform noise and filter processing on the two-dimensional topography map, switch to three-dimensional topography, Figure 4 The three-dimensional topography diagram of the V-shaped hole area of the galvanized layer is given, Figure 4 The alloy layer between the galv...
Embodiment 3
[0054] The color-coated steel plate is used, and the thickness of the color-coated primer is measured by combining V-shaped drilling and laser confocal technology.
[0055] 1) Use a conical head with a taper of 60° to drill a V-shaped hole on the surface of the color-coated steel plate with a depth of 0.15mm.
[0056] 2) Focus on the V-shaped hole area in the visible light mode of the laser confocal microscope, and enter the laser mode after it is clear.
[0057] 3) Scan layer by layer in laser mode to obtain the two-dimensional shape of the V-shaped hole.
[0058] 4) Perform noise and filter processing on the two-dimensional topography map, switch to three-dimensional topography, and obtain the three-dimensional topography map of the V-shaped hole.
[0059] 5) Directly select the measurement point of the junction of the color-coated topcoat and the primer and the measurement point of the junction of the primer and the substrate to measure the height difference, so as to obta...
PUM
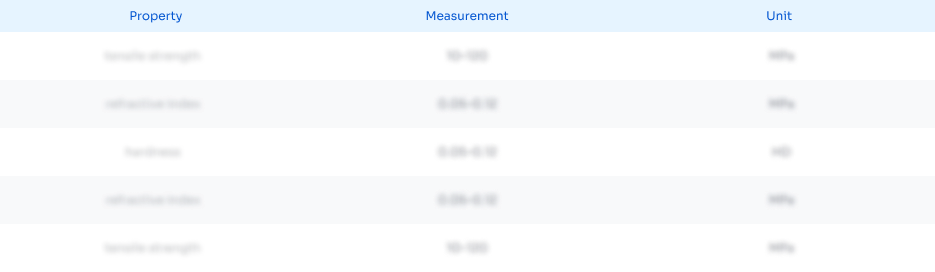
Abstract
Description
Claims
Application Information

- R&D
- Intellectual Property
- Life Sciences
- Materials
- Tech Scout
- Unparalleled Data Quality
- Higher Quality Content
- 60% Fewer Hallucinations
Browse by: Latest US Patents, China's latest patents, Technical Efficacy Thesaurus, Application Domain, Technology Topic, Popular Technical Reports.
© 2025 PatSnap. All rights reserved.Legal|Privacy policy|Modern Slavery Act Transparency Statement|Sitemap|About US| Contact US: help@patsnap.com