Polyurethane resin for synthetic leather with high water pressure resistance
A polyurethane resin and polyester diol technology, which is applied in the field of polyurethane resin for high water pressure resistant synthetic leather, can solve the problems of low water pressure resistance, increased consumption of raw materials, poor hand feeling, etc., and achieve excellent water pressure resistance and excellent water resistance Effect
- Summary
- Abstract
- Description
- Claims
- Application Information
AI Technical Summary
Problems solved by technology
Method used
Image
Examples
Embodiment 1
[0027] A polyurethane resin for high water pressure resistant synthetic leather, made from the following raw materials:
[0028]
[0029] This polyurethane resin adopts the preparation method of following steps to make:
[0030] 1) Dissolve 120Kg of polyneopentyl adipate diol with a molecular weight of 2000, 120Kg of polytetrahydrofuran ether diol with a molecular weight of 1000, and 5Kg of ethylene glycol that have been melted into liquid by heating in 267Kg of N,N-dimethyl In a mixture of formamide and 200Kg toluene, stir evenly at 70°C and keep warm for 15 minutes;
[0031] 2) Add 65Kg of 4,4'-diphenylmethane diisocyanate and keep it warm at 70°C for 2 hours;
[0032] 3) Add 0.01Kg organic bismuth catalyst to gradually increase the viscosity of the system;
[0033] 4) After the viscosity of the system reaches 300Pa.s, add a mixture of 133Kg N,N-dimethylformamide and 100Kg toluene, and then add 0.1Kg methanol;
[0034] 5) Cool down to 60°C, keep warm and stir for 0.5 h...
Embodiment 2
[0036] A polyurethane resin for high water pressure resistant synthetic leather, made from the following raw materials:
[0037]
[0038] This polyurethane resin adopts the preparation method of following steps to make:
[0039] 1) 60Kg of neopentyl glycol adipate diol with a molecular weight of 1000, 40Kg of polymethylpropylene adipate diol with a molecular weight of 1000, 100Kg of polypropylene glycol with a molecular weight of 2000 and Dissolve 10Kg of ethylene glycol in a mixture of 267Kg N,N-dimethylformamide and 180Kg methyl ethyl ketone, stir evenly at 75°C, and keep warm for 15 minutes;
[0040] 2) Add 78Kg of 4,4'-diphenylmethane diisocyanate and keep it warm at 75°C for 2 hours;
[0041] 3) Add 0.03Kg organic bismuth catalyst to gradually increase the viscosity of the system;
[0042] 4) After the viscosity of the system reaches 350Pa.s, add a mixture of 133Kg N,N-dimethylformamide and 90Kg methyl ethyl ketone, and then add 0.3Kg methanol;
[0043] 5) Cool down...
Embodiment 3
[0045] A polyurethane resin for high water pressure resistant synthetic leather, made from the following raw materials:
[0046]
[0047] This polyurethane resin adopts the preparation method of following steps to make:
[0048] 1) 60Kg of polyneopentyl adipate diol with a molecular weight of 2000, 20Kg of polybutylene adipate diol with a molecular weight of 2000, and 40Kg of polytetrahydrofuran ether with a molecular weight of 2000 that have been melted into a liquid state by heating Diol, 40Kg polypropylene glycol with a molecular weight of 2000 and 15Kg ethylene glycol were dissolved in a mixture of 200Kg N,N-dimethylformamide, 133Kg methyl ethyl ketone and 67Kg toluene, stirred evenly at 80°C, and kept warm for 15 minutes;
[0049] 2) Add 80Kg of 4,4'-diphenylmethane diisocyanate and keep it warm at 80°C for 2 hours;
[0050] 3) Add 0.05Kg organic bismuth catalyst to gradually increase the viscosity of the system;
[0051] 4) After the viscosity of the system reaches ...
PUM
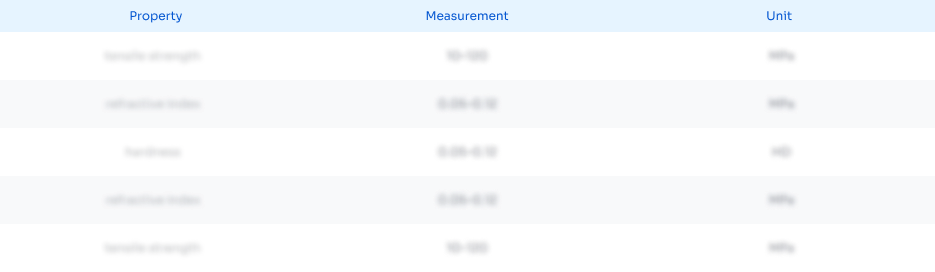
Abstract
Description
Claims
Application Information

- Generate Ideas
- Intellectual Property
- Life Sciences
- Materials
- Tech Scout
- Unparalleled Data Quality
- Higher Quality Content
- 60% Fewer Hallucinations
Browse by: Latest US Patents, China's latest patents, Technical Efficacy Thesaurus, Application Domain, Technology Topic, Popular Technical Reports.
© 2025 PatSnap. All rights reserved.Legal|Privacy policy|Modern Slavery Act Transparency Statement|Sitemap|About US| Contact US: help@patsnap.com