Preparation method for novel ethylene propylene rubber sealing material product
An ethylene-propylene rubber and sealing material technology, applied in chemical instruments and methods, other chemical processes and other directions, can solve the problems of product aging resistance, high production cost, poor flame retardant performance, etc., and achieves easy industrialization and implementation. The effect of high production efficiency and short curing time
- Summary
- Abstract
- Description
- Claims
- Application Information
AI Technical Summary
Problems solved by technology
Method used
Examples
Embodiment 1
[0018] (1) Weigh 6Kg EPDM 4436, 5.5Kg EPDM 539, 10Kg carbon black, 3Kg light calcium carbonate, 9Kg paraffin oil, 0.5Kg zinc oxide, 0.1Kg stearic acid, 0.1Kg KY-405, 0.05Kg of MBZ, 0.1Kg of polyethylene glycol, 0.1Kg of polyethylene wax, 0.15Kg of AFLUX-42. In addition, weigh 0.15Kg accelerator CZ, 0.15Kg accelerator BZ, 0.05Kg accelerator TRA, 0.05Kg accelerator TT, 0.05Kg accelerator PZ, 0.1Kg sulfur, and 0.15Kg ammonium polyphosphate.
[0019] (2) Put ethylene propylene rubber in an internal mixer for 60 seconds, then add zinc oxide, stearic acid, KY-405, MBZ and mix for 40 seconds, add carbon black, light calcium carbonate, paraffin oil, Polyethylene glycol, polyethylene wax, and AFLUX-42 are banburyed for 120 seconds to obtain a section of glue. The temperature of mastication and mixing is controlled at 130°C.
[0020] (3) Put a section of rubber on the open mill, add accelerators CZ, BZ, TRA, TT, PZ, vulcanizing agent sulfur and flame retardant ammonium polyphosphate, ...
Embodiment 2
[0023] (1) Weigh 6Kg EPDM 4436, 5.5Kg EPDM 539, 12Kg carbon black, 3.3Kg light calcium carbonate, 9Kg paraffin oil, 0.5Kg zinc oxide, 0.15Kg stearic acid, 0.1Kg KY-405, MBZ 0.05Kg, Polyethylene Glycol 0.1Kg, Polyethylene Wax 0.1Kg, AFLUX-42 0.15Kg. In addition, weigh 0.2Kg accelerator CZ, 0.15Kg accelerator BZ, 0.05Kg accelerator TRA, 0.05Kg accelerator TT, 0.05Kg accelerator PZ, 0.1Kg sulfur, and 0.15Kg TCEP.
[0024] (2) Put ethylene propylene rubber in an internal mixer for 80 seconds, then add zinc oxide, stearic acid, KY-405, MBZ and mix for 40 seconds, add carbon black, light calcium carbonate, paraffin oil, Polyethylene glycol, polyethylene wax, and AFLUX-42 are banburyed for 120 seconds to obtain a section of glue. The temperature of mastication and mixing is controlled at 120°C.
[0025] (3) Put a section of rubber on the open mill, add accelerators CZ, BZ, TRA, TT, PZ, vulcanizing agent sulfur and flame retardant ammonium polyphosphate, and knead at 60°C until the ...
Embodiment 3
[0028] (1) Weigh 6Kg EPDM 4436, 5Kg EPDM 539, 12.5Kg carbon black, 4Kg light calcium carbonate, 9Kg paraffin oil, 0.5Kg zinc oxide, 0.15Kg stearic acid, 0.1Kg KY-405, 0.05Kg of MBZ, 0.1Kg of polyethylene glycol, 0.1Kg of polyethylene wax, 0.15Kg of AFLUX-42. In addition, weigh 0.2Kg accelerator CZ, 0.15Kg accelerator BZ, 0.05Kg accelerator TRA, 0.05Kg accelerator TT, 0.05Kg accelerator PZ, 0.2Kg sulfur, and 0.2Kg TCPP.
[0029] (2) Put ethylene propylene rubber in an internal mixer for 70 seconds, then add zinc oxide, stearic acid, KY-405, MBZ and mix for 30 seconds, add carbon black, light calcium carbonate, paraffin oil, Polyethylene glycol, polyethylene wax, and AFLUX-42 are banburyed for 120 seconds to obtain a section of glue. The temperature of mastication and mixing is controlled at 130°C.
[0030] (3) Put a section of rubber on the open mill, add accelerators CZ, BZ, TRA, TT, PZ, vulcanizing agent sulfur and flame retardant ammonium polyphosphate, and knead at 55°C u...
PUM
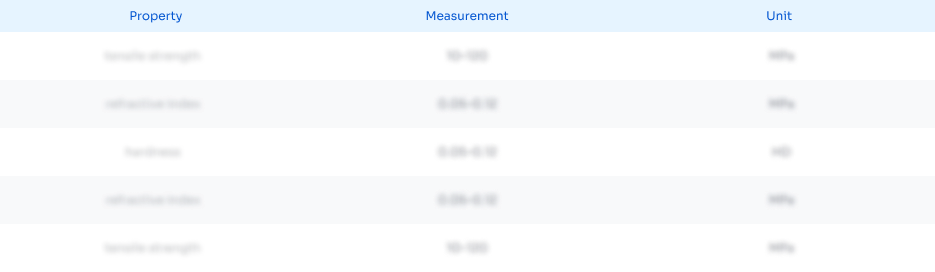
Abstract
Description
Claims
Application Information

- R&D
- Intellectual Property
- Life Sciences
- Materials
- Tech Scout
- Unparalleled Data Quality
- Higher Quality Content
- 60% Fewer Hallucinations
Browse by: Latest US Patents, China's latest patents, Technical Efficacy Thesaurus, Application Domain, Technology Topic, Popular Technical Reports.
© 2025 PatSnap. All rights reserved.Legal|Privacy policy|Modern Slavery Act Transparency Statement|Sitemap|About US| Contact US: help@patsnap.com