Purification technique of biodegradable polyesters
A technology for degrading polyester and process, which is applied in the field of polymers and pharmacy, can solve problems such as yield reduction, and achieve the effects of improving stability, ensuring degradation, and ensuring stability
- Summary
- Abstract
- Description
- Claims
- Application Information
AI Technical Summary
Problems solved by technology
Method used
Image
Examples
Embodiment 1
[0034]Example 1: Take poly(D,L)-lactide glycolide (75:25) (Mw=82500, Mn=45800, Mw / Mn=1.8) 50g, dissolved in acetonitrile to make a solution with a concentration of 1.5g / 100ml (W / V), adding petroleum ether in different proportions (see Table 1 for the volume ratio) for extraction: use an axial stirrer to Stir at 1300rpm for 30min to form droplets with a particle size of less than 500μm, then let stand to separate the layers, separate the petroleum ether layer, repeat the extraction 3 times, take the acetonitrile phase and filter it through a 0.22μm microporous membrane, and vacuum concentrate the filtrate to 12g / 100ml. Take amyl alcohol equivalent to 15 times the volume of the concentrated solution, slowly pour the concentrated solution into the amyl alcohol, and stir continuously until the solid precipitates; remove the amyl alcohol solution, add the same volume of absolute ethanol, stir and ultrasonically treat for 20 minutes, replace The same volume of absolute ethanol, st...
Embodiment 2
[0037] Example 2: Take 50 g of polyglycolide (Mw=12100, Mn=6370, Mw / Mn=1.9) prepared by reaction (with lauryl alcohol as the molecular weight regulator and stannous octoate as the catalyst), add acetonitrile to dissolve Make a solution (W / V) with a concentration of 8g / 100ml, add petroleum ether according to the volume ratio of acetonitrile:petroleum ether = 1:9 for extraction: stir with an axial stirrer for 30min to form droplets with a particle size of less than 800μm, statically After standing, the layers were separated, the petroleum ether layer was separated, and the extraction was repeated 5 times. The acetonitrile phase was filtered through a 0.22 μm microporous membrane under pressure, and the filtrate was concentrated in vacuo to 20 g / 100 ml. After taking 10 times, 20 times, and 30 times the volume of ethanol equivalent to the volume of the polyglycolide concentrated solution, slowly pour the polyglycolide concentrated solution into the ethanol, stirring continuously un...
Embodiment 3
[0040] Example 3: Take 50 g of poly(D)-lactide (Mw=297000, Mn=174700, Mw / Mn=1.7) prepared by reaction (using glycolic acid as molecular weight regulator and stannous octoate as catalyst), add After dissolving acetonitrile, make a solution (W / V) with a concentration of 0.05g / 100ml, and add petroleum ether according to the ratio of acetonitrile: petroleum ether = volume ratio 1:4 for extraction: Stir with an axial stirrer for 30 minutes and then let it stand to separate The petroleum ether layer was separated, and the extraction was repeated 10 times. The acetonitrile phase was filtered through a 0.22 μm microporous membrane under pressure, and the filtrate was concentrated in vacuo to 8 g / 100 ml. After taking 1,2-propanediol equivalent to 25 times the volume of the polylactide concentrate, slowly pour the polylactide concentrate into the 1,2-propanediol, stirring continuously until solids are precipitated; remove 1,2-propanediol solution, add the same volume of absolute ethanol...
PUM
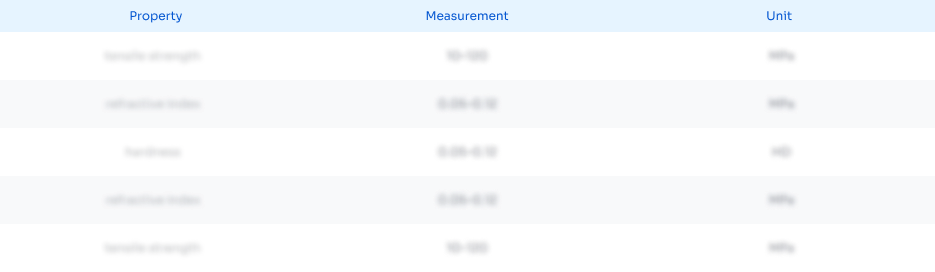
Abstract
Description
Claims
Application Information

- R&D
- Intellectual Property
- Life Sciences
- Materials
- Tech Scout
- Unparalleled Data Quality
- Higher Quality Content
- 60% Fewer Hallucinations
Browse by: Latest US Patents, China's latest patents, Technical Efficacy Thesaurus, Application Domain, Technology Topic, Popular Technical Reports.
© 2025 PatSnap. All rights reserved.Legal|Privacy policy|Modern Slavery Act Transparency Statement|Sitemap|About US| Contact US: help@patsnap.com