Method for low-temperature preparation of anatase titanium dioxide film on surface of cotton fabric
An anatase titanium dioxide and titanium dioxide technology, which is applied in the directions of plant fibers, textiles and papermaking, fiber processing, etc., can solve the problems of high cost of high-frequency electric field heating, unsuitable for large-scale production in factories, etc., and achieves low preparation temperature and raw material cost. Low cost and high photocatalytic performance
- Summary
- Abstract
- Description
- Claims
- Application Information
AI Technical Summary
Problems solved by technology
Method used
Image
Examples
Embodiment 1
[0028] Mix 3mL of absolute ethanol, 6mL of glacial acetic acid and 10mL of tetra-n-butyl titanate, then slowly add it dropwise to 120mL of a mixed solution of acetic acid and water with a pH of 2.5 for hydrolysis, and form a light yellow color after vigorous stirring transparent sol.
[0029] Soak the pretreated cotton fabric in titanium dioxide sol for 3 minutes, dip twice and roll it twice (the liquid rolling rate is 80%), pre-dry it at 80°C for 3 minutes, steam it in a steam box at 100°C for 3 hours, and finish drying the cotton fabric. The process of preparing titanium dioxide film on the surface of fabric.
[0030] According to the national standard GB / T8629-2001 "Household Washing and Drying Procedures for Textile Testing", the titanium dioxide modified cotton fabrics were washed and dried (type A washing machine, 5A washing procedure, A-type drying procedure), after 50 times of washing Finally, characterize the XRD pattern of the film, see figure 1 . The test results...
Embodiment 2
[0032] Mix 3mL of absolute ethanol, 6mL of glacial acetic acid and 10mL of tetra-n-butyl titanate, then slowly add it dropwise to 120mL of a mixed solution of acetic acid and water with a pH of 2.5 for hydrolysis, and form a light yellow color after vigorous stirring transparent sol.
[0033] Soak the pretreated cotton fabric in titanium dioxide sol for 3 minutes, dip twice and roll it twice (the liquid rolling rate is 80%), pre-dry it at 80°C for 3 minutes, steam it in a steam box at 100°C for 3 hours, and finish drying the cotton fabric. The process of preparing titanium dioxide film on the surface of fabric.
[0034] According to the national standard GB / T8629-2001 "Household Washing and Drying Procedures for Textile Testing", the titanium dioxide modified cotton fabrics were washed and dried (type A washing machine, 5A washing procedure, A-type drying procedure), after 50 times of washing Finally, the film-forming state of the fabric surface was characterized by scanning ...
Embodiment 3
[0036] Mix 3mL of absolute ethanol, 6mL of glacial acetic acid and 10mL of tetra-n-butyl titanate, then slowly add it dropwise to 120mL of a mixed solution of acetic acid and water with a pH of 2.5 for hydrolysis, and form a light yellow color after vigorous stirring transparent sol.
[0037] Soak the pretreated cotton fabric in titanium dioxide sol for 3 minutes, dip twice and roll it twice (the liquid rolling rate is 80%), pre-dry it at 80°C for 3 minutes, steam it in a steam box at 100°C for 3 hours, and finish drying the cotton fabric. The process of preparing titanium dioxide film on the surface of fabric.
[0038] According to the national standard GB / T8629-2001 "Household Washing and Drying Procedures for Textile Testing", the titanium dioxide modified cotton fabrics were washed and dried (type A washing machine, 5A washing procedure, A-type drying procedure), after 50 times of washing Finally, the fabric prepared with titanium dioxide film was placed in a closed conta...
PUM
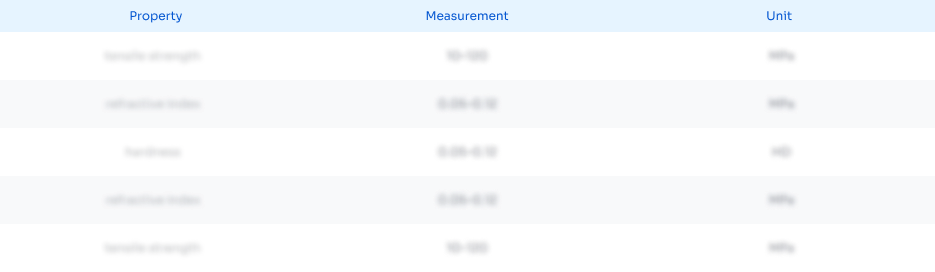
Abstract
Description
Claims
Application Information

- R&D
- Intellectual Property
- Life Sciences
- Materials
- Tech Scout
- Unparalleled Data Quality
- Higher Quality Content
- 60% Fewer Hallucinations
Browse by: Latest US Patents, China's latest patents, Technical Efficacy Thesaurus, Application Domain, Technology Topic, Popular Technical Reports.
© 2025 PatSnap. All rights reserved.Legal|Privacy policy|Modern Slavery Act Transparency Statement|Sitemap|About US| Contact US: help@patsnap.com