Preparation method for PVC-based carbon nanofiber
A technology of carbon nanofibers and nitrogen nitrogen dimethylformamide, which is applied in fiber processing, fiber chemical characteristics, textiles and papermaking, etc., can solve the problem of small hydrogen absorption, difficulty in determining the hydrogen absorption position, and difficulty in making suitable microstructures. Problems such as pore volume, shape and material, to achieve the effect of easy operation, easy recovery, and simple equipment
- Summary
- Abstract
- Description
- Claims
- Application Information
AI Technical Summary
Problems solved by technology
Method used
Image
Examples
Embodiment 1
[0031] 1. Preparation of electrospinning solution: Mix 1.4g PVC (K value 72-71), 0.0560g nickel chloride and 18.6mL nitrodimethylformamide, and stir for a period of time at 50 °C to form a uniform spinning liquid.
[0032] 2. Through electrospinning equipment, under the conditions of voltage 25KV, feeding flow rate of spinning solution 0.6mL / h, and electrospinning temperature 35℃, spinning solution electrospinning to prepare PVC / NiCl 2 Composite nanofiber precursors.
[0033] 3. The prepared PVC / NiCl 2 The composite nanofiber precursors were dried in an oven (temperature 50 °C) for 8 h.
[0034] 4. PVC / NiCl after drying 2 The composite nanofiber precursors were treated with iodine vapor under vacuum and 80°C for 48h.
[0035] 5. After the above iodine pretreatment, the nanofibers were calcined in a muffle furnace at 320 °C for 1 h
[0036] 6. The pre-oxidized nanofibers were calcined in a tube furnace at a nitrogen flow rate of 300ml / min at 2°C / min to 1000°C for 1 hour t...
Embodiment 2
[0039] 1. Preparation of electrospinning solution: Mix 1.4g PVC (K value 72-71), 0.0560g nickel chloride and 18.6mL nitrodimethylformamide, and stir for a period of time at 50 °C to form a uniform spinning liquid.
[0040] 2. Through electrospinning equipment, under the conditions of voltage 25KV, feeding flow rate of spinning solution 0.6mL / h, and electrospinning temperature 35℃, spinning solution electrospinning to prepare PVC / NiCl 2 Composite nanofiber precursors.
[0041] 3. The prepared PVC / NiCl 2 The composite nanofiber precursors were dried in an oven (temperature 50 °C) for 8 h.
[0042] 4. PVC / NiCl after drying 2 The composite nanofiber precursors were treated in alkaline solution (6.25mol / L sodium hydroxide, 0.037mol / L tetrabutylammonium bromide) at 70°C for 24h.
[0043] 5. The nanofibers were calcined in a muffle furnace at 260 °C for 3 h after the above alkali pretreatment.
[0044] 6. The pre-oxidized nanofibers were calcined in a tube furnace at a nitrogen...
Embodiment 3
[0046] 1. Preparation of electrospinning solution: Mix 1.4g PVC (K value 72-71), 0.0560g nickel acetate and 18.6mL nitrodimethylformamide, and stir for a period of time at 50°C to form a uniform spinning solution .
[0047] 2. Through electrospinning equipment, under the conditions of voltage 25KV, feeding flow rate of spinning solution 0.6mL / h, and electrospinning temperature 35℃, spinning solution electrospinning to prepare PVC / (CH) 3 COO) 2 Ni composite nanofiber precursors.
[0048] 3. The prepared PVC / (CH 3 COO) 2 The Ni composite nanofiber precursors were dried in an oven (temperature 50 °C) for 8 h.
[0049] 4. PVC / (CH after drying 3 COO) 2 The precursors of Ni composite nanofibers were treated with iodine vapor at 80 °C for 48 h in vacuum.
[0050] 5. After the above iodine pretreatment, the nanofibers were calcined in a muffle furnace at 320 °C for 1 h.
[0051] 6. The above pre-oxidized nanofibers are calcined in a tube furnace at a nitrogen flow rate of 300ml / ...
PUM
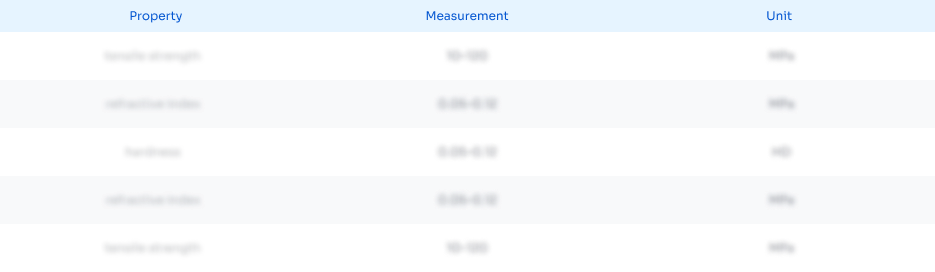
Abstract
Description
Claims
Application Information

- Generate Ideas
- Intellectual Property
- Life Sciences
- Materials
- Tech Scout
- Unparalleled Data Quality
- Higher Quality Content
- 60% Fewer Hallucinations
Browse by: Latest US Patents, China's latest patents, Technical Efficacy Thesaurus, Application Domain, Technology Topic, Popular Technical Reports.
© 2025 PatSnap. All rights reserved.Legal|Privacy policy|Modern Slavery Act Transparency Statement|Sitemap|About US| Contact US: help@patsnap.com