Waste oil-based environment-friendly mold separating agent and preparation method thereof
A waste oil, environment-friendly technology, applied in the direction of manufacturing tools, unloading devices, lubricating compositions, etc., can solve the problems of general demoulding effect, environmental health hazards, and high cost, achieve good demoulding effect, reduce production costs, smooth surface effect
- Summary
- Abstract
- Description
- Claims
- Application Information
AI Technical Summary
Problems solved by technology
Method used
Examples
Embodiment 1
[0021] (1) Weigh the raw materials according to the following weight proportions: 300Kg of waste oil, 70Kg of Tween 60, 20Kg of alkylphenol polyoxyethylene ether, 10Kg of spherical natural graphite with a particle size of less than 10μm, and 600Kg of water; (2) Weigh Add 300Kg of half the weight of water in the formula system to the stainless steel reactor, stir at 100 rpm, heat up to 60°C, and then add 70Kg of Tween 60 and 20Kg of alkylphenol polyoxyethylene ether in sequence , stirred for 30 minutes to form a mixed solution M-1; (3) In another reactor, add 300Kg of waste oil and under the condition of 100-300 rpm, add 10Kg of sliding components with a particle size of less than 10μm spherical For natural graphite, stir for 30 minutes, then heat up to 90-100°C, react for 1 hour, and form a mixed solution M-2; (4) Pour the mixed solution M-2 into the mixed solution M-1, and keep the stirring speed at 100-300 Turn / min, after mixing and stirring for 10 minutes, heat to 90-10...
Embodiment 2
[0023] (1) Weigh the raw materials according to the following weight ratio: 200Kg of waste oil, 100Kg of Tween 20, 50Kg of alkylphenol polyoxyethylene ether, 20Kg of spherical natural graphite with a particle size of less than 10μm, and 630Kg of water; (2) Weigh Add 315Kg of half the weight of water in the formula system into the stainless steel reactor, stir at 100 rpm, heat up to 60°C, and then add 100Kg of Tween 20 and 50Kg of alkylphenol polyoxyethylene ether in sequence, Stir for 30 minutes to form a mixed solution M-1; (3) In another reaction kettle, add 200Kg of waste oil and under the condition of 100-300 rpm, add 20Kg of spherical natural stone with a sliding component particle size less than 10μm Ink, stir for 30 minutes, then raise the temperature to 90-100°C, react for 1 hour, and form a mixed solution M-2; (4) Pour the mixed solution M-2 into the mixed solution M-1, and keep the stirring speed at 100-300 rpm / min, after mixing and stirring for 10min, heat to 9...
Embodiment 3
[0025] (1) Weigh the raw materials according to the following weight ratio: 400Kg of waste oil, 50Kg of Tween 80, 10Kg of fatty alcohol polyoxyethylene ether, 10Kg of spherical natural graphite with a particle size of less than 10μm, and 539Kg of water; Add 269.5Kg of half the weight of water in the formula system into a stainless steel reactor, stir at 100 rpm, heat up to 60°C, then add 50Kg of Tween 80 and 10Kg of fatty alcohol polyoxyethylene ether in sequence, Stir for 30 minutes to form a mixed solution M-1; (3) In another reaction kettle, add 400Kg of waste oil and under the condition of 100-300 rpm, add 1Kg of spherical natural stone with a sliding component particle size less than 10μm Ink, stir for 30 minutes, then raise the temperature to 90-100°C, react for 1 hour, and form a mixed solution M-2; (4) Pour the mixed solution M-2 into the mixed solution M-1, and keep the stirring speed at 100-300 rpm / min, after mixing and stirring for 10min, heat to 90-100°C, then...
PUM
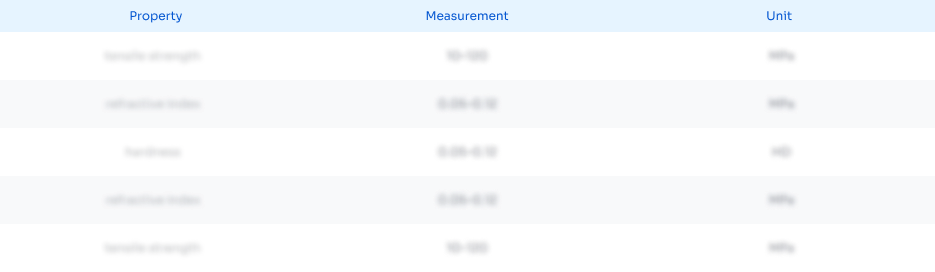
Abstract
Description
Claims
Application Information

- R&D
- Intellectual Property
- Life Sciences
- Materials
- Tech Scout
- Unparalleled Data Quality
- Higher Quality Content
- 60% Fewer Hallucinations
Browse by: Latest US Patents, China's latest patents, Technical Efficacy Thesaurus, Application Domain, Technology Topic, Popular Technical Reports.
© 2025 PatSnap. All rights reserved.Legal|Privacy policy|Modern Slavery Act Transparency Statement|Sitemap|About US| Contact US: help@patsnap.com