The preparation method of sucrose ester
A technology of sucrose ester and sucrose, applied in the field of non-ionic surfactants, can solve the problems of unguaranteed product quality, complicated separation and purification steps, easy to generate a large amount of waste water, etc., to achieve product safety, simple pretreatment method, and satisfactory Purity and non-toxic properties of the required effect
- Summary
- Abstract
- Description
- Claims
- Application Information
AI Technical Summary
Problems solved by technology
Method used
Image
Examples
Embodiment 1
[0022] 4g of calcium oxide is added in 30g methyl stearate as dewatering agent, stir, remove a small amount of water and free fatty acid in methyl stearate, then the methyl stearate after dewatering is transferred to three-necked bottle , add 51g of crushed and ground sucrose, use 3.2g of calcium oxide as a catalyst, stir and disperse evenly for 30 minutes, adjust and set the oil bath temperature to 130°C, synthesize sucrose ester under normal pressure or reduced pressure, and continue stirring. After the reaction was carried out for 4 hours, the heating was stopped, the product was filtered to remove the catalyst, the reaction solution was transferred to a separatory funnel, the layers were left to stand, the lower water phase was removed, and the upper oil phase was washed with distilled water until it was neutral. The purer sucrose ester can be obtained by vacuum distillation of the product at ℃.
Embodiment 2
[0024] 6g calcium oxide is added in 36g methyl stearate as dewatering agent, stir, remove a small amount of water and free fatty acid in methyl stearate, then the methyl stearate after dewatering is transferred to three-necked bottle Add 103g of crushed and ground sucrose, use 6.9g of calcium oxide as a catalyst, stir and disperse evenly for 30 minutes, adjust and set the oil bath temperature to 90°C, synthesize sucrose ester under normal pressure or reduced pressure, and continue stirring. After the reaction was carried out for 2 hours, the heating was stopped, the product was filtered to remove the solid catalyst, the reaction solution was transferred to a separatory funnel, and the layers were left to stand, the lower water phase was removed, and the upper oil phase was washed with distilled water until it was neutral, and then in Purified sucrose esters can be obtained by vacuum distillation of the product at 80°C.
Embodiment 3
[0026] 7g calcium oxide is added in 42g methyl stearate as dewatering agent, stir, remove a small amount of water and free fatty acid in methyl stearate, then the methyl stearate after dewatering is transferred to three-necked bottle In the process, add 217g of crushed and ground sucrose, use 15.5g of calcium oxide as a catalyst, stir and disperse evenly for 30 minutes, adjust and set the oil bath temperature to 160°C, synthesize sucrose ester under normal pressure or reduced pressure, and continue stirring After the reaction is carried out for 42 hours, the heating is stopped, the product is filtered to remove the solid catalyst, the reaction solution is transferred to a separatory funnel, the layers are left to stand, the lower water phase is removed, and the upper oil phase is washed with distilled water until it is neutral, and then Purified sucrose esters can be obtained by distilling the product under reduced pressure at 80°C.
PUM
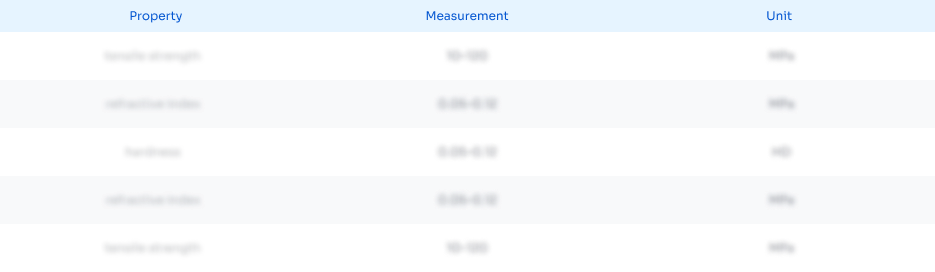
Abstract
Description
Claims
Application Information

- R&D
- Intellectual Property
- Life Sciences
- Materials
- Tech Scout
- Unparalleled Data Quality
- Higher Quality Content
- 60% Fewer Hallucinations
Browse by: Latest US Patents, China's latest patents, Technical Efficacy Thesaurus, Application Domain, Technology Topic, Popular Technical Reports.
© 2025 PatSnap. All rights reserved.Legal|Privacy policy|Modern Slavery Act Transparency Statement|Sitemap|About US| Contact US: help@patsnap.com