UCM six-roller mill
A technology of six-high rolling mill and work roll, applied in the direction of roll, metal rolling, metal rolling, etc., can solve the problems of high equipment cost, increased production cost, large edge loss, etc., to reduce the trimming amount of finished products and improve finished products rate effect
- Summary
- Abstract
- Description
- Claims
- Application Information
AI Technical Summary
Problems solved by technology
Method used
Image
Examples
Embodiment Construction
[0013] Such as figure 1 As shown, the UCM six-high rolling mill of the present invention includes fixed rolls 1, intermediate rolls 2 and work rolls 3 arranged up and down in sequence, and the ends of the work rolls 3 are provided with chamfers; the chamfers at the ends of the work rolls 3 are The taper width L1 of the chamfer is 30 mm, and the taper height He of the chamfer is 60 microns.
[0014] The working process of this example: because the work rolls cannot move laterally, during the rolling process of the silicon steel plate 4, the width L2 of the taper from the edge to the chamfer is 40 mm, which can effectively reduce the convexity of the rolled plate and the edge thinning area .
[0015] An embodiment of the present invention has been described in detail above, but the content described is only a preferred embodiment of the present invention, and cannot be considered as limiting the implementation scope of the present invention. All equivalent changes and improvem...
PUM
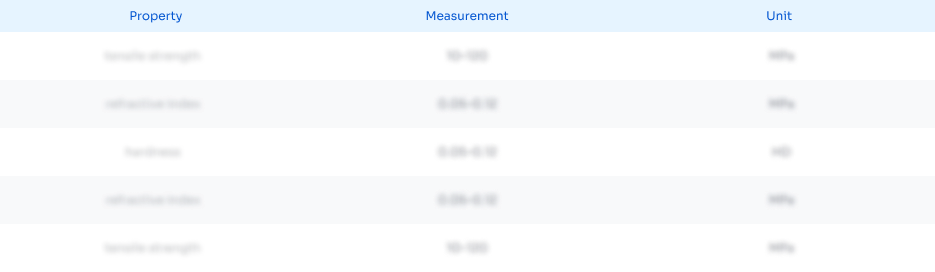
Abstract
Description
Claims
Application Information

- Generate Ideas
- Intellectual Property
- Life Sciences
- Materials
- Tech Scout
- Unparalleled Data Quality
- Higher Quality Content
- 60% Fewer Hallucinations
Browse by: Latest US Patents, China's latest patents, Technical Efficacy Thesaurus, Application Domain, Technology Topic, Popular Technical Reports.
© 2025 PatSnap. All rights reserved.Legal|Privacy policy|Modern Slavery Act Transparency Statement|Sitemap|About US| Contact US: help@patsnap.com