Technology capable of improving tension of main grid of photoinductive electroplating battery
A light-induced electroplating and busbar technology, which is applied in the direction of sustainable manufacturing/processing, circuits, electrical components, etc., can solve the problem of poor pulling force at the welding part of the busbar, the impact of the electroplating grid line battery market, and desoldering at the busbar, etc. problem, to achieve good ohmic contact and adhesion, good pull-off force, and low unit consumption
- Summary
- Abstract
- Description
- Claims
- Application Information
AI Technical Summary
Problems solved by technology
Method used
Examples
Embodiment 1
[0017] Clean the silicon wafer, remove the damaged layer, and make texture; put the silicon wafer into a tubular diffusion furnace for diffusion, the resistance after diffusion is 80Ω / port, and the junction depth is 0.3μm; remove the phosphosilicate glass from the diffused silicon wafer and Remove the back junction; deposit a silicon nitride passivation anti-reflection layer on the surface of the emitter, and screen-print the back electrode and the back electric field. Use corrosion slurry or laser slotting, activate the slot with a lower concentration of HF, then electroplate a layer of thin nickel with a thickness of about 2um as a primer, sinter at 300°C for 3 minutes in a low-temperature oxygen-containing 3% environment, and finally electroplate copper and silver. After drying, the test busbar tension is 1.8N-2.4N, unqualified, and the electrical performance is good.
Embodiment 2
[0019] Clean the silicon wafer, remove the damaged layer, and make texture; put the silicon wafer into a tubular diffusion furnace for diffusion, the resistance after diffusion is 80Ω / port, and the junction depth is 0.3μm; remove the phosphosilicate glass from the diffused silicon wafer and Remove the back junction; deposit a silicon nitride passivation anti-reflection layer on the surface of the emitter, and screen-print the back electrode and the back electric field. Use corrosion paste or laser slotting, activate the slot with a lower concentration of HF, then electroplate a layer of thin nickel with a thickness of about 2um as a primer, then print 0.04g of low-temperature silver paste at the position of the main grid, bake at 120-200°C for 10min, and then Sinter at 280°C for 3 minutes in a low-temperature environment containing 3% oxygen, and finally electroplate copper and silver. After drying, the test busbar tension is 2.4N-2.9N, barely qualified, and the series connect...
Embodiment 3
[0021] Clean the silicon wafer, remove the damaged layer, and make texture; put the silicon wafer into a tubular diffusion furnace for diffusion, the resistance after diffusion is 80Ω / port, and the junction depth is 0.3μm; remove the phosphosilicate glass from the diffused silicon wafer and Remove the back junction; deposit a silicon nitride passivation anti-reflection layer on the surface of the emitter, and screen-print the back electrode and the back electric field. Use corrosion paste or laser slotting, activate the slot with a lower concentration of HF, then electroplate a layer of thin nickel with a thickness of about 2um as a primer, then print 0.05g of low-temperature silver paste at the position of the main grid, bake at 120-200°C for 10min, and then Sinter at 300°C for 3 minutes in an environment containing 3% oxygen, and finally electroplate copper and silver. After drying, the test busbar tension is 4.5N-5N, which is qualified and the electrical performance is good...
PUM
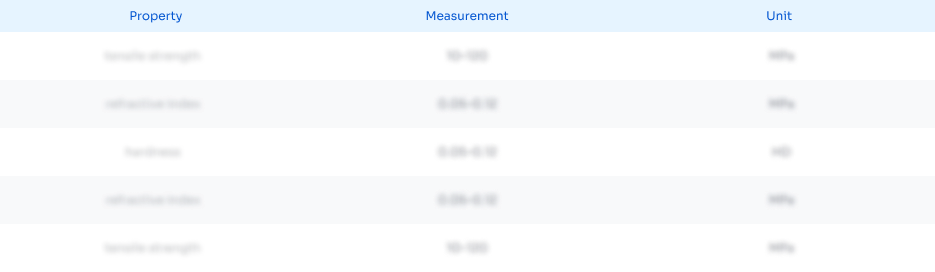
Abstract
Description
Claims
Application Information

- Generate Ideas
- Intellectual Property
- Life Sciences
- Materials
- Tech Scout
- Unparalleled Data Quality
- Higher Quality Content
- 60% Fewer Hallucinations
Browse by: Latest US Patents, China's latest patents, Technical Efficacy Thesaurus, Application Domain, Technology Topic, Popular Technical Reports.
© 2025 PatSnap. All rights reserved.Legal|Privacy policy|Modern Slavery Act Transparency Statement|Sitemap|About US| Contact US: help@patsnap.com