Stabilizer bar bushing and preparation method thereof
The technology of a stabilizer bar bushing and a stabilizer is applied to the bushing on the lateral stabilizer bar of an automobile suspension and the field of preparation thereof, which can solve the problems of affecting performance, dust sticking to lubricating grease, rubber without lubricating function, etc., so as to solve the problem of noise problems, reducing friction, and good wear resistance
- Summary
- Abstract
- Description
- Claims
- Application Information
AI Technical Summary
Problems solved by technology
Method used
Image
Examples
Embodiment 1
[0062] A stabilizer bushing, which comprises the following raw materials in parts by weight:
[0063]
[0064]
[0065] The preparation method of the above-mentioned stabilizer bushing comprises the following steps:
[0066] (1) Use the above formula to prepare the raw materials, and send the raw materials into the internal mixer, the mixing time is 4 to 6 minutes, and the glue is removed at 110°C to obtain synthetic rubber;
[0067] (2) The above-mentioned synthetic rubber is kneaded and formed in an open mill at a temperature of 60-70°C to obtain a strip-shaped molded part;
[0068] (3) Put the strip-shaped molding into the barrel of the injection vulcanizer, and perform vulcanization treatment under the conditions of a pressure of 170-190kgf / cm2 and a temperature of 160-170°C. The vulcanization time is 240-360 seconds, cooling, Stabilizer bushing after trimming.
Embodiment 2
[0070] A stabilizer bushing, which comprises the following raw materials in parts by weight:
[0071]
[0072]
[0073] Its preparation method is identical with embodiment 1.
Embodiment 3
[0075] A stabilizer bushing, which comprises the following raw materials in parts by weight:
[0076]
[0077]
[0078] Its preparation method is identical with embodiment 1.
[0079] In the above-mentioned Examples 1-3, imported fatty acid and microcrystalline wax B-10 were used as lubricants, Plasthall 7050 which had poor compatibility with natural rubber was used as plasticizer, and high wear-resistant carbon black N326 was used as reinforcing agent. This design uses Plasthall 7050 as a plasticizer which is incompatible in natural rubber and precipitates out on the surface of the product. At the same time, the lubricant component is brought out to the surface of the product, so that the friction force between the product and the metal is very small, and the friction noise is eliminated. The added high wear-resistant carbon black N326 can improve the mechanical strength of the product, improve the wear resistance, and meet the product life requirements.
PUM
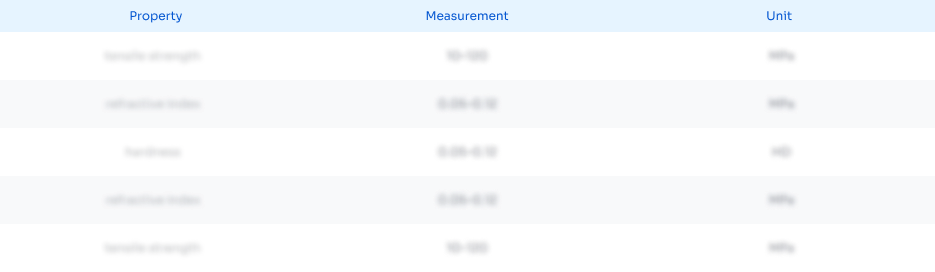
Abstract
Description
Claims
Application Information

- R&D
- Intellectual Property
- Life Sciences
- Materials
- Tech Scout
- Unparalleled Data Quality
- Higher Quality Content
- 60% Fewer Hallucinations
Browse by: Latest US Patents, China's latest patents, Technical Efficacy Thesaurus, Application Domain, Technology Topic, Popular Technical Reports.
© 2025 PatSnap. All rights reserved.Legal|Privacy policy|Modern Slavery Act Transparency Statement|Sitemap|About US| Contact US: help@patsnap.com