Manufacturing method for diesel engine exhaust valve upper seat
A manufacturing method and exhaust valve technology, which is applied in the manufacturing field of diesel engine parts, can solve problems such as difficulty in ensuring relative positions, and achieve the effects of difficult clamping, high coaxiality, and improved quality and efficiency
- Summary
- Abstract
- Description
- Claims
- Application Information
AI Technical Summary
Problems solved by technology
Method used
Image
Examples
Embodiment
[0034] Embodiment: a kind of manufacturing method of diesel engine exhaust valve upper seat, concrete steps are as follows:
[0035] Step 1. Grinding the non-processed surface of the blank;
[0036] Step 2. Machining the center hole on the end surface of the inner hole of the first hole 1 of the lathe;
[0037] Step 3. Based on the central hole and the outer circle at the end with the larger diameter of the blank, draw the plane lines, circular lines, and lap processing lines, and check the blank allowance;
[0038] Step 4. The four claws of the lathe clamp the outer circle of the end with the larger diameter, correct it, and rough turn the inner hole of the first hole 1 to the process positioning size;
[0039] Step 5, milling the first, second, third and fourth circles D, E, F, G;
[0040] Step 6, Rough turning the second outer circle 2, the third, fourth and fifth holes 3, 4, 5, the first step 8 and the undercut;
[0041] Step 7. Subsequent adjustment of the large outer ...
PUM
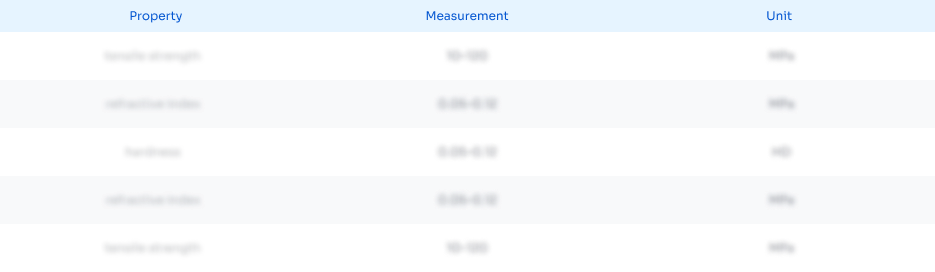
Abstract
Description
Claims
Application Information

- R&D Engineer
- R&D Manager
- IP Professional
- Industry Leading Data Capabilities
- Powerful AI technology
- Patent DNA Extraction
Browse by: Latest US Patents, China's latest patents, Technical Efficacy Thesaurus, Application Domain, Technology Topic, Popular Technical Reports.
© 2024 PatSnap. All rights reserved.Legal|Privacy policy|Modern Slavery Act Transparency Statement|Sitemap|About US| Contact US: help@patsnap.com