Method for making patterning conducting layer
A technology for patterning conductive layers and conductive layers, which is applied in chemical/electrolytic methods to remove conductive materials, multilayer circuit manufacturing, and secondary processing of printed circuits, etc., which can solve problems such as complicated processes, difficult processes, and a lot of time spent , to achieve the effect of shortening the process time and simplifying the process steps
- Summary
- Abstract
- Description
- Claims
- Application Information
AI Technical Summary
Problems solved by technology
Method used
Image
Examples
Embodiment Construction
[0024] In order to make the above objects, features and advantages of the present invention more comprehensible, specific implementations of the present invention will be described in detail below in conjunction with the accompanying drawings. First of all, it should be noted that the present invention is not limited to the following specific embodiments. Those skilled in the art should understand the present invention from the spirit embodied in the following embodiments, and each technical term can be optimized based on the spirit of the present invention. broad understanding. The same or similar components in the figures are denoted by the same reference numerals.
[0025] refer to figure 2 The method for making a patterned conductive layer in a preferred embodiment of the present invention is to coat a conductive film on the surface of a substrate 31 in conjunction with a roll-to-roll process, and etch the film into a predetermined pattern. The roll-to-roll process is t...
PUM
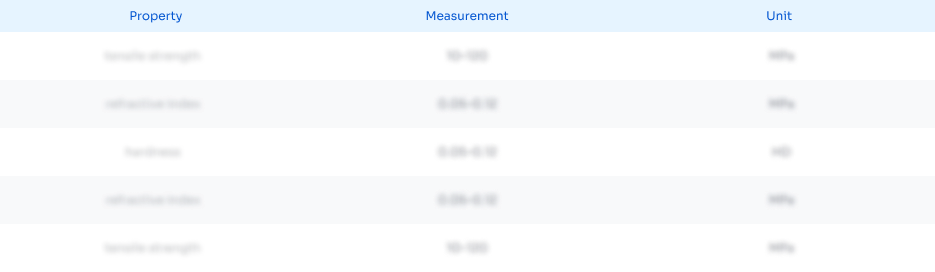
Abstract
Description
Claims
Application Information

- R&D Engineer
- R&D Manager
- IP Professional
- Industry Leading Data Capabilities
- Powerful AI technology
- Patent DNA Extraction
Browse by: Latest US Patents, China's latest patents, Technical Efficacy Thesaurus, Application Domain, Technology Topic, Popular Technical Reports.
© 2024 PatSnap. All rights reserved.Legal|Privacy policy|Modern Slavery Act Transparency Statement|Sitemap|About US| Contact US: help@patsnap.com