Rapid solving method for failure workspace of six-degree-of-freedom parallel robot
A work space and robot technology, applied in instruments, simulators, computer control, etc., can solve problems such as low computing efficiency, poor applicability, and difficulty, and achieve the effects of reducing measurement costs, improving control performance, and reducing the number of iterations
- Summary
- Abstract
- Description
- Claims
- Application Information
AI Technical Summary
Problems solved by technology
Method used
Image
Examples
Embodiment Construction
[0039] The present invention will be described in further detail below with reference to the accompanying drawings.
[0040] refer to figure 1 , the invention assists in debugging using a six-degree-of-freedom parallel robot model and MATLAB software.
[0041] Such as figure 1 As shown, the global coordinate system is established with the center of the base platform and the center of the motion platform as the origin and the local coordinate system . respectively The center position of a Hooke hinge and a spherical hinge. use express exist The position vector in , express exist The position vector in .
[0042] vector is the position vector of the moving platform center p in the global coordinate system, Indicates the position and attitude of the moving platform, then the first i The vector of each outrigger in global coordinates is:
[0043] (1)
[0044] In the formula, R for p - xyz relatively O - ...
PUM
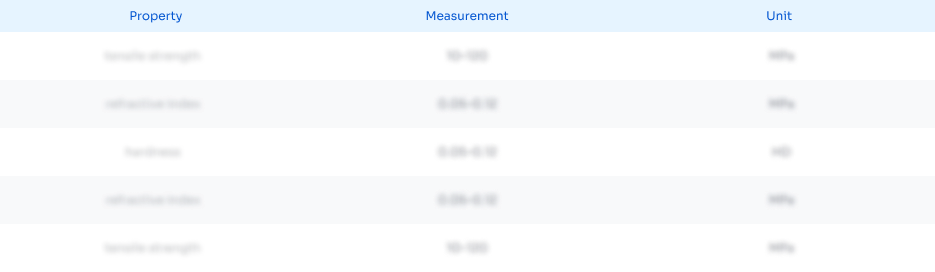
Abstract
Description
Claims
Application Information

- R&D
- Intellectual Property
- Life Sciences
- Materials
- Tech Scout
- Unparalleled Data Quality
- Higher Quality Content
- 60% Fewer Hallucinations
Browse by: Latest US Patents, China's latest patents, Technical Efficacy Thesaurus, Application Domain, Technology Topic, Popular Technical Reports.
© 2025 PatSnap. All rights reserved.Legal|Privacy policy|Modern Slavery Act Transparency Statement|Sitemap|About US| Contact US: help@patsnap.com