Melt polycondensation method, special reactor and falling-film elements
A technology of polycondensation reactor and melt polycondensation, which is applied in chemical/physical/physical chemical fixed reactors, chemical instruments and methods, chemical/physical/physical chemical processes, etc., can solve the problem of insufficient homogenization and mixing of melts and film formation Low efficiency, wide molecular weight distribution and other problems, to achieve the effect of uniform melt residence time, uniform reaction temperature and narrow molecular weight distribution
- Summary
- Abstract
- Description
- Claims
- Application Information
AI Technical Summary
Problems solved by technology
Method used
Image
Examples
Embodiment Construction
[0035] A kind of melting polycondensation reactor provided by the present invention, such as figure 1 As shown, it includes: a vertical housing 7, a head 1 connected to the upper end of the vertical housing 7 and a bottom shell 14 at the lower end, the top of the head 1 is provided with a feed port 26, and the top of the vertical housing 7 is provided with Vacuum suction port 19, the bottom of the bottom shell 14 is provided with a discharge port 13; the upper end of the vertical housing 7 is connected and installed with a cylindrical box 4 through fasteners, and the cylindrical box 4 is composed of an upper cover plate 2 and a middle partition 3 and the bottom plate 5 are divided into two layers of boxes, the upper box communicates with the heat transfer medium inlet 22, the lower box communicates with the heat transfer medium outlet 21, and a storage tray 6 is hung below the cylindrical box body 4, and the storage tray 6 is connected to the heat transfer medium outlet 21. Th...
PUM
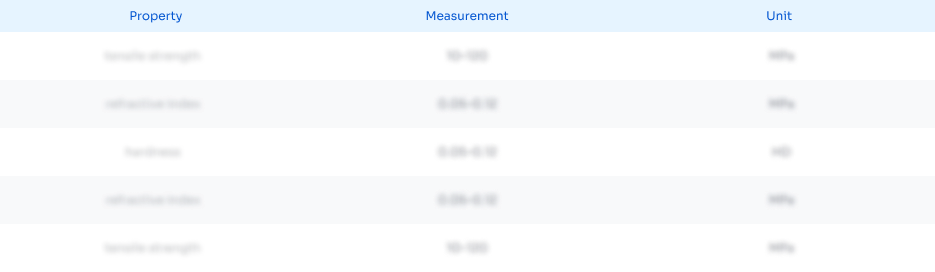
Abstract
Description
Claims
Application Information

- R&D
- Intellectual Property
- Life Sciences
- Materials
- Tech Scout
- Unparalleled Data Quality
- Higher Quality Content
- 60% Fewer Hallucinations
Browse by: Latest US Patents, China's latest patents, Technical Efficacy Thesaurus, Application Domain, Technology Topic, Popular Technical Reports.
© 2025 PatSnap. All rights reserved.Legal|Privacy policy|Modern Slavery Act Transparency Statement|Sitemap|About US| Contact US: help@patsnap.com