The preparation method of sucrose ester
A technology of sucrose ester and sucrose, applied in the field of non-ionic surfactants, can solve the problems of low thermal stability, product coking and agglomeration, affecting product quality, etc., and achieves high monoester content, good product quality, and good emulsifying performance. Effect
- Summary
- Abstract
- Description
- Claims
- Application Information
AI Technical Summary
Problems solved by technology
Method used
Image
Examples
Embodiment 1
[0018] Calcium oxide and sodium hydroxide were burned at 700°C for 2 hours, and cooled for later use; methyl stearate was heated and melted, and the calcium oxide burned in step (1) was added to stir, and filtered after stirring; step (2 ) filtered methyl stearate, sucrose and step (1) burnt sodium hydroxide are placed in a reaction vessel, fully mixed, stirred and reacted in an oil bath for 1 hour, the temperature during the reaction The temperature is 120°C, the stirring speed is 800rpmm, and the pressure is 0.005MPa; the product obtained in step (3) is washed with butanone several times, and after vacuum drying, the present sucrose ester is obtained with a yield of 74.1%.
[0019] The consumption of described sodium hydroxide is 4% of described methyl stearate quality; The mol ratio of described methyl stearate and sucrose is 3:1; The consumption of described calcium oxide is described methyl stearate 10% of ester mass.
Embodiment 2
[0021] Calcium oxide and sodium hydroxide were burned at 800°C for 3 hours, cooled for later use; methyl stearate was heated and melted, and the calcium oxide burned in step (1) was added to stir, and filtered after stirring; step (2 ) the filtered methyl stearate, sucrose and step (1) burning sodium hydroxide are placed in a reaction vessel, fully mixed, stirred and reacted in an oil bath for 2 hours, the temperature during the reaction The temperature is 130°C, the stirring speed is 900rpmm, and the pressure is 0.010MPa; the product obtained in step (3) is washed with butanone several times, and after vacuum drying, the present sucrose ester is obtained with a yield of 75.4%.
[0022] The consumption of described sodium hydroxide is 6% of described methyl stearate quality; The mol ratio of described methyl stearate and sucrose is 3:1; The consumption of described calcium oxide is described methyl stearate 12% of ester mass.
Embodiment 3
[0024] Calcium oxide and sodium hydroxide were burned at 900°C for 4 hours, cooled for later use; methyl stearate was heated and melted, and the calcium oxide burned in step (1) was added to stir, and filtered after stirring; step (2 ) the filtered methyl stearate, sucrose and step (1) burnt sodium hydroxide are placed in a reaction vessel, fully mixed, and stirred and reacted in an oil bath for 3 hours. During the reaction, the temperature The temperature is 150°C, the stirring speed is 1000rpmm, and the pressure is 0.020MPa; the product obtained in step (3) is washed with butanone several times, and after vacuum drying, the present sucrose ester is obtained with a yield of 76.9%.
[0025] The consumption of described sodium hydroxide is 8% of described methyl stearate quality; The mol ratio of described methyl stearate and sucrose is 3:1; The consumption of described calcium oxide is described methyl stearate 14% of ester mass.
PUM
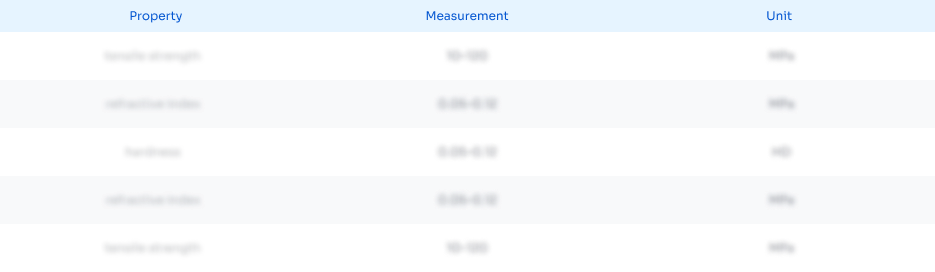
Abstract
Description
Claims
Application Information

- R&D
- Intellectual Property
- Life Sciences
- Materials
- Tech Scout
- Unparalleled Data Quality
- Higher Quality Content
- 60% Fewer Hallucinations
Browse by: Latest US Patents, China's latest patents, Technical Efficacy Thesaurus, Application Domain, Technology Topic, Popular Technical Reports.
© 2025 PatSnap. All rights reserved.Legal|Privacy policy|Modern Slavery Act Transparency Statement|Sitemap|About US| Contact US: help@patsnap.com