Wet-process flue gas desulfurization tower
A wet flue gas desulfurization and tower technology, which is applied in separation methods, chemical instruments and methods, and dispersed particle separation, etc., can solve the problems of poor atomization effect of washing liquid, unsatisfactory dehydration effect, and low probability of nozzle blockage. , to increase the tower section coverage, avoid flue gas channeling, and improve work reliability.
- Summary
- Abstract
- Description
- Claims
- Application Information
AI Technical Summary
Problems solved by technology
Method used
Image
Examples
Embodiment 1
[0033] The sulfur-containing flue gas enters from the flue gas inlet 2 at the lower part of the tower body 1, and rises through a bubble desulfurization zone composed of a sieve plate 3 with a plurality of micropores. When the liquid film of the desulfurization slurry meets, a large number of bubbles are formed, and the bubbles burst to arouse water droplets, water spray, water mist, etc., so that the flue gas can fully contact the slurry, and a part of the sulfur dioxide in the flue gas is absorbed by the desulfurization slurry. The flue gas continues to rise through the liquid mist desulfurization area, and the slurry supply pipe 7 transports the desulfurization slurry to a plurality of low-pressure atomizing nozzles 4 with a short double-helix large flow channel structure, and sprays the desulfurization slurry downward. The short double-helix large flow channel structure The low-pressure atomizing nozzle 4 is composed of a nozzle sleeve 4a and a nozzle core 4b. The bottom of...
Embodiment 2
[0036] The sulfur-containing flue gas enters from the flue gas inlet 2 at the lower part of the tower body 1, and rises through the bubble desulfurization zone composed of two layers of sieve plates 3 with multiple micropores. When the liquid film of the desulfurization slurry meets, a large number of bubbles are formed, and the bubbles burst to arouse water droplets, water spray, water mist, etc., so that the flue gas can fully contact the slurry, and a part of the sulfur dioxide in the flue gas is absorbed by the desulfurization slurry. The flue gas continues to rise through the liquid mist desulfurization area, and the slurry supply pipe 7 transports the desulfurization slurry to a plurality of low-pressure atomizing nozzles 4 with a short double-helix large flow channel structure, and sprays the desulfurization slurry downward. The short double-helix large flow channel structure The low-pressure atomizing nozzle 4 is composed of a nozzle sleeve 4a and a nozzle core 4b. The ...
Embodiment 3
[0040] The sulfur-containing flue gas enters from the flue gas inlet 2 at the lower part of the tower body 1, and rises through a bubble desulfurization zone composed of a sieve plate 3 with a plurality of micropores. The liquid films of the prepared desulfurization slurry meet to form a large number of bubbles, and the bubbles burst to arouse water droplets, water spray, water mist, etc., so that the flue gas can fully contact the slurry, and a part of the sulfur dioxide in the flue gas is absorbed by the desulfurization slurry. The flue gas continues to rise through the liquid mist desulfurization area, and the slurry supply pipe 7 transports the desulfurization slurry to a plurality of low-pressure atomizing nozzles 4 with a short double-helix large flow channel structure, and sprays the desulfurization slurry downward. The short double-helix large flow channel structure The low-pressure atomizing nozzle 4 is composed of a nozzle sleeve 4a and a nozzle core 4b. The bottom of...
PUM
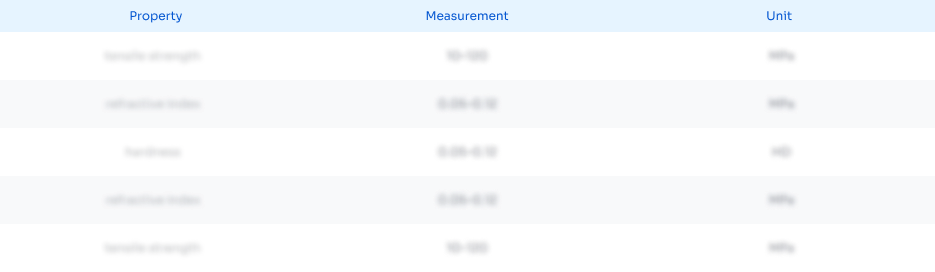
Abstract
Description
Claims
Application Information

- R&D
- Intellectual Property
- Life Sciences
- Materials
- Tech Scout
- Unparalleled Data Quality
- Higher Quality Content
- 60% Fewer Hallucinations
Browse by: Latest US Patents, China's latest patents, Technical Efficacy Thesaurus, Application Domain, Technology Topic, Popular Technical Reports.
© 2025 PatSnap. All rights reserved.Legal|Privacy policy|Modern Slavery Act Transparency Statement|Sitemap|About US| Contact US: help@patsnap.com