Polycrystalline silicon ingotting furnace and ingotting method thereof
A technology of polysilicon ingot casting furnace and ingot casting, which is applied to the growth of polycrystalline materials, chemical instruments and methods, crystal growth, etc., can solve the problems of slow heating rate of silicon liquid, shortened thermal field life, and limitation of silicon material temperature rise, etc., to achieve The effect of shortening ingot casting time, increasing production capacity, and large process window
- Summary
- Abstract
- Description
- Claims
- Application Information
AI Technical Summary
Problems solved by technology
Method used
Image
Examples
Embodiment Construction
[0029] Such as figure 1 As shown, a polysilicon ingot furnace includes a furnace body insulation layer 1, a top heater 2, a quartz crucible 3, a cooling platform 4 and a heat dissipation window 5, and also includes a bottom heater 6, which is located at the bottom Describe the underside of the cooling platform 4. Such as figure 2 As shown, the bottom heater 6 includes a common terminal 61, an A-phase electrode 62, a B-phase electrode 63, a C-phase electrode 64 and a heater 65, and the A-phase electrode, B-phase electrode and C-phase electrode pass through the heater 65 Connect to the common terminal 61.
[0030] A polysilicon ingot casting method, comprising the steps of heating, melting, directional crystallization, annealing and cooling, characterized in that the heating step is:
[0031] (1) The duration is 9-11 minutes, set the power output of the top heater to 10%, set the power output of the bottom heater to 10%, vacuum mode, the air intake is zero, and the heater i...
PUM
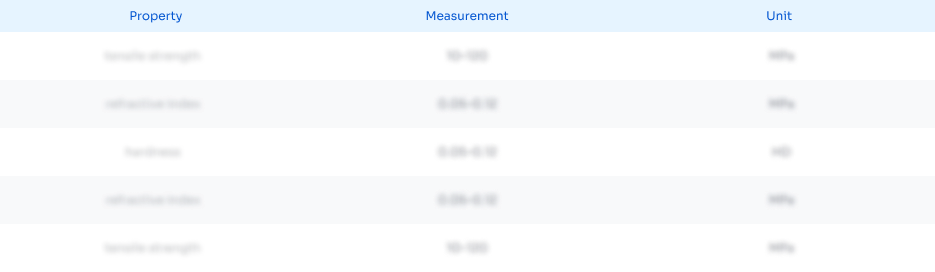
Abstract
Description
Claims
Application Information

- Generate Ideas
- Intellectual Property
- Life Sciences
- Materials
- Tech Scout
- Unparalleled Data Quality
- Higher Quality Content
- 60% Fewer Hallucinations
Browse by: Latest US Patents, China's latest patents, Technical Efficacy Thesaurus, Application Domain, Technology Topic, Popular Technical Reports.
© 2025 PatSnap. All rights reserved.Legal|Privacy policy|Modern Slavery Act Transparency Statement|Sitemap|About US| Contact US: help@patsnap.com