Method for achieving forming of GH4738 nickel-base superalloy turbine discs
A technology of nickel-based high-temperature alloy and turbine disk, which is applied in the direction of engine components and mechanical equipment, can solve the problems of complex process and low efficiency, and achieve the effect of uniform grain size, stable operation and good grain structure
- Summary
- Abstract
- Description
- Claims
- Application Information
AI Technical Summary
Problems solved by technology
Method used
Image
Examples
Embodiment 1
[0034] Embodiment 1: This embodiment proposes a method for realizing the forming of a GH4738 nickel-based superalloy turbine disk, and obtains better performance, which is characterized in that it specifically includes the following steps:
[0035] step 1:
[0036] 1) The regular Φ110mm×260mm cylindrical rod blank is hard-coated, the initial grain size is 150μm, and the actual composition of the selected GH4738 alloy is measured as C: 0.06; Al: 1.42; Ti: 3.15; Co: 13.5; Cr: 20.0; Mo: 4.1; Ni balance. a. First wrap the bar firmly with thermal insulation cotton; b. Then use a cut stainless steel plate (thickness 0.8mm) to hard wrap the outer side of the thermal insulation cotton, and weld the connection firmly.
[0037] 2) Heat the sheathed bar: a. Put the bar in the effective area of the electric furnace, pad it with refractory bricks below, and control the heating temperature at 1080°C; b. Connect the external armored couple to the K type as required galvanic couple.
[0...
Embodiment 2
[0051] Embodiment 2: This embodiment proposes a method for realizing the forming of a GH4738 nickel-based superalloy turbine disk, and obtains better performance, which is characterized in that it specifically includes the following steps:
[0052] step 1:
[0053] 1) The regular Φ102mm×270mm cylindrical rod blank is hard-coated, the initial grain size is 160μm, and the actual composition of the selected GH4738 alloy is measured as C: 0.04; Al: 1.39; Ti: 3.05; Co: 13.3; Cr: 19.8; Mo: 4.05; Ni balance. a. First wrap the bar firmly with thermal insulation cotton; b. Then use a cut stainless steel plate (thickness 0.8mm) to hard wrap the outer side of the thermal insulation cotton, and weld the connection firmly.
[0054] 2) Heat the sheathed bar: a. Put the bar in the effective area of the electric furnace, pad it with refractory bricks below, and control the heating temperature at 1060°C; b. Connect the external armored couple to the K type as required galvanic couple.
[...
Embodiment 3
[0063] This embodiment proposes a method to realize the forming of GH4738 nickel-based superalloy turbine disc, and obtains better performance. The difference between the forming process and Example 1 lies in step (2): the cake base obtained in step 1 is subjected to the following die forging process Control: a. Firstly, hard wrap the biscuit as shown in 1); b. Put the wrapped biscuit in the effective area of the electric furnace, pad it with refractory bricks below, and control the heating temperature at 1080°C ; c. Connect the external armored couple as required, K-type galvanic couple; d. After adjusting the preheated mold on the press, use water lubricant to lubricate the mold cavity to ensure that the temperature is above 350 ° C; e. After the forging billet reaches the set temperature completely, the cake is quickly transferred to the mold of the press after being released from the furnace, and the cake is placed in the middle of the mold, and the transfer time is contr...
PUM
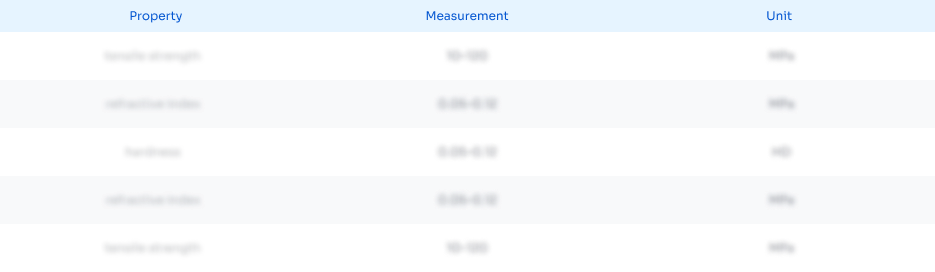
Abstract
Description
Claims
Application Information

- R&D
- Intellectual Property
- Life Sciences
- Materials
- Tech Scout
- Unparalleled Data Quality
- Higher Quality Content
- 60% Fewer Hallucinations
Browse by: Latest US Patents, China's latest patents, Technical Efficacy Thesaurus, Application Domain, Technology Topic, Popular Technical Reports.
© 2025 PatSnap. All rights reserved.Legal|Privacy policy|Modern Slavery Act Transparency Statement|Sitemap|About US| Contact US: help@patsnap.com