Pump fiber combiner manufacturing method for large power fiber laser
A fiber laser and pump fiber technology, applied in the field of optical fiber, can solve the problems of large signal light loss, increased temperature of the beam combiner, low pump light absorption rate, etc., to achieve enhanced anti-reflection ability, small signal insertion loss, The effect of high pumping efficiency
- Summary
- Abstract
- Description
- Claims
- Application Information
AI Technical Summary
Problems solved by technology
Method used
Image
Examples
Embodiment 1
[0028] Depend on image 3 Known, the manufacture method of the pump fiber beam combiner that is used for high-power fiber laser, comprises the following steps: 1, by image 3 a know, choose a section of quartz capillary 301, its inner diameter φ1 is just equal to the outer diameter of the inner cladding of the double-clad optical fiber, and the outer diameter φ2 of the quartz capillary depends on the number of pumping fibers required (such as 25 / 250 optical fiber, the inner diameter of the tube is 250 μm ; Such as 20 / 400 optical fiber, the inner diameter of the tube is 400μm).
[0029] 2. Use vertical polishing method to process quartz capillary, see image 3 b. Use a conical polishing machine to polish one end of the quartz capillary, and control the conical angle to 2θ to obtain image 3 The quartz capillary 201 shown in b has a conical shape at one end and a planar shape at the other end.
[0030] 3. Thread a plurality of pumping optical fibers 202 into a porous metal o...
Embodiment 2
[0034] Depend on Image 6 It is known that the manufacturing method of the pumping fiber combiner for high-power fiber lasers uses horizontal polishing to process the quartz capillary so that one end is conical, and the rest of the steps are the same as in Example 1.
Embodiment 3
[0036] Depend on Figure 7 It is known that the manufacturing method of the pump fiber combiner used for high-power fiber lasers is to put the cylindrical quartz capillary vertically into the hydrofluoric acid (HF) solution by hydrofluoric acid etching method, and slowly lift it to make the outer surface of the quartz capillary It is corroded into a conical shape, and one end of the processed quartz capillary is conical. In order to prevent the inner wall of the capillary from being corroded, it is necessary to coat an antiseptic on the inner wall of the capillary in advance; the remaining steps are the same as in Example 1.
PUM
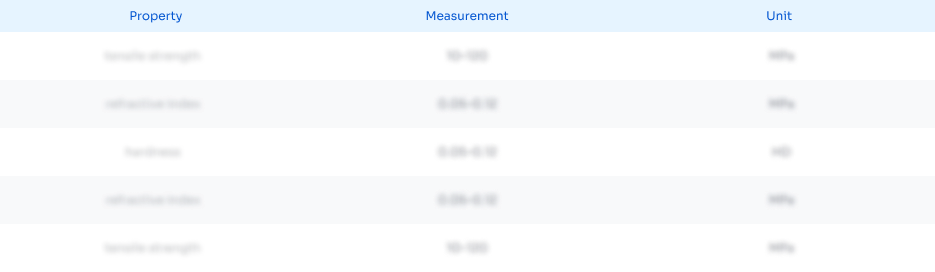
Abstract
Description
Claims
Application Information

- Generate Ideas
- Intellectual Property
- Life Sciences
- Materials
- Tech Scout
- Unparalleled Data Quality
- Higher Quality Content
- 60% Fewer Hallucinations
Browse by: Latest US Patents, China's latest patents, Technical Efficacy Thesaurus, Application Domain, Technology Topic, Popular Technical Reports.
© 2025 PatSnap. All rights reserved.Legal|Privacy policy|Modern Slavery Act Transparency Statement|Sitemap|About US| Contact US: help@patsnap.com