Modular sensor and manufacturing technique thereof
A manufacturing process and sensor technology, applied in the field of sensors, can solve the problems of poor product design flexibility, poor product versatility, broken and plugged PIN pins, and no signal detected by the sensor, so as to avoid damage to electronic components, ensure firm positioning, and ensure The effect of sensing breath
- Summary
- Abstract
- Description
- Claims
- Application Information
AI Technical Summary
Problems solved by technology
Method used
Image
Examples
Embodiment Construction
[0082] The present invention will be further described in detail below in conjunction with the accompanying drawings and specific embodiments.
[0083] The modular sensor provided by the present invention is mainly used for active sensors, such as figure 2 , image 3 and Figure 4 As shown, it includes a cavity module 1 , a skeleton module 2 , a circuit board, a Hall chip 4 and a cover plate 8 , wherein the circuit board takes a flexible circuit board 3 as an example.
[0084] Such as Figure 5 As shown, the cavity module 1 is a shell with an open top. There is a positioning groove 12 in the middle of the bottom of the shell. The left and right sides of the positioning groove 12 are polished; the bottom of the shell is integrally molded with a PIN needle assembly 11 (eg Figure 11 shown), the PIN needle assembly 11 has three obtuse-angled PIN needles 111, 112, 113, one end of which protrudes from one side of the cavity module 1, and the other end protrudes obliquely upwar...
PUM
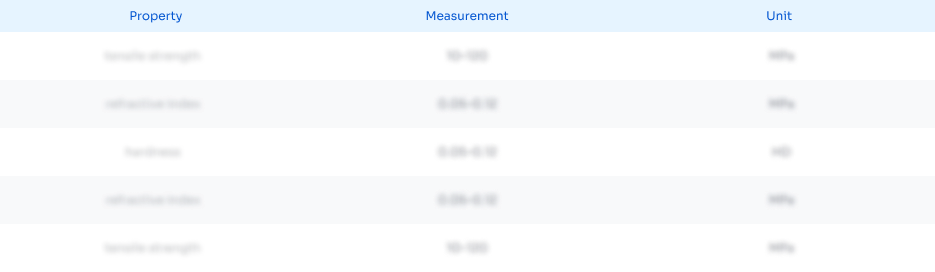
Abstract
Description
Claims
Application Information

- R&D
- Intellectual Property
- Life Sciences
- Materials
- Tech Scout
- Unparalleled Data Quality
- Higher Quality Content
- 60% Fewer Hallucinations
Browse by: Latest US Patents, China's latest patents, Technical Efficacy Thesaurus, Application Domain, Technology Topic, Popular Technical Reports.
© 2025 PatSnap. All rights reserved.Legal|Privacy policy|Modern Slavery Act Transparency Statement|Sitemap|About US| Contact US: help@patsnap.com