Wind Turbine Blade Vibration Control Method Using Composite Damping Structure
A technology of wind turbine blades and composite damping, which is applied in wind turbines, engines, wind power generation, etc. It can solve the problems of lack of prevention and control methods, and the flutter of large flexible blades of wind turbines is easy to occur, so as to achieve good vibration suppression performance and improve aerodynamic stability Sexuality, the effect of increasing production costs
- Summary
- Abstract
- Description
- Claims
- Application Information
AI Technical Summary
Problems solved by technology
Method used
Image
Examples
Embodiment 1
[0055] Take a certain 2500kW wind turbine as an example. The wind turbine is mainly used in offshore wind farms. Its design power is 2.5MW and it adopts three-blade form. The material of the leaf skin is GRP. The main design parameters are shown in Table 1.
[0056] Table 1 Main Design Parameters
[0057]
[0058] (1) airfoil selection
[0059] According to the design requirements, the NACA6413 airfoil is selected for all blades, which has a large lift-to-drag ratio and good stall performance.
[0060] (2) Damping structure
[0061] Composite materials, damping materials, and co-cured constrained damping layer structure of composite materials are used; I-beam steel beams are used for the main beam, and the free damping layer is treated, that is, the damping material is pasted on the web of the main beam with epoxy resin. Epoxy viscoelastic material (SMRD100F50) is selected as the damping material, and its loss factor β =0.89, and can withstand the temperature of 120°C ...
PUM
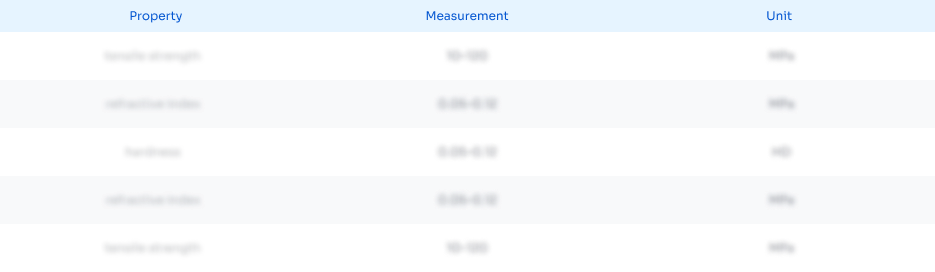
Abstract
Description
Claims
Application Information

- Generate Ideas
- Intellectual Property
- Life Sciences
- Materials
- Tech Scout
- Unparalleled Data Quality
- Higher Quality Content
- 60% Fewer Hallucinations
Browse by: Latest US Patents, China's latest patents, Technical Efficacy Thesaurus, Application Domain, Technology Topic, Popular Technical Reports.
© 2025 PatSnap. All rights reserved.Legal|Privacy policy|Modern Slavery Act Transparency Statement|Sitemap|About US| Contact US: help@patsnap.com