Converter steelmaking method and converter steelmaking device
A converter steelmaking and gas source technology, applied in the manufacture of converters, etc., can solve the problems of large consumption of oxygen and coke, more slag overflow, and large consumption of oxygen, so as to reduce the consumption of coal and coke, ensure the transmission concentration, Continuous and uniform effect of powder spraying
- Summary
- Abstract
- Description
- Claims
- Application Information
AI Technical Summary
Problems solved by technology
Method used
Image
Examples
Embodiment 2
[0026] Such as figure 1 A kind of converter steelmaking device as shown, comprises blowing tank 4, mixer 7, conveying pipeline, secondary mixer 8 and special spray gun connected successively by blowing pipeline; The parts are horizontally connected to the inflation pipeline Ⅰ and the inflation pipeline Ⅱ5 equipped with the regulating valve 6, wherein the elbow of the mixer 7 is a large-angle elbow, and the elbow is made of an elbow lined with wear-resistant ceramic material, and the secondary mixer 8 and A distributor 9 and a powder spraying branch pipe 10 are installed between the special spray guns.
[0027] During operation, the dry high-grade concentrate powder with a moisture content of 0.7% and an iron content of 68% is weighed and then sent from the silo 1 to the injection tank 4, and the injection tank 4 is passed through a valve equipped with a regulating valve 6. Inflatable pipeline Ⅰ and nitrogen pipeline Ⅱ5 are connected to two gas sources, the gas source is nitro...
PUM
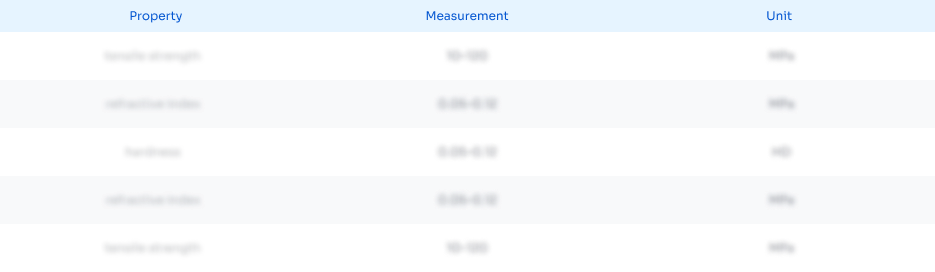
Abstract
Description
Claims
Application Information

- R&D Engineer
- R&D Manager
- IP Professional
- Industry Leading Data Capabilities
- Powerful AI technology
- Patent DNA Extraction
Browse by: Latest US Patents, China's latest patents, Technical Efficacy Thesaurus, Application Domain, Technology Topic.
© 2024 PatSnap. All rights reserved.Legal|Privacy policy|Modern Slavery Act Transparency Statement|Sitemap