Engine room soundproof wall mounting structure for railway vehicle
A technology for rail vehicles and installation structures, applied in railway car body, transportation and packaging, railway car body parts, etc., can solve the problems of difficult alignment, difficult process assurance, poor sound insulation effect of sound insulation walls, etc. Good torsion performance and the effect of improving sound insulation performance
- Summary
- Abstract
- Description
- Claims
- Application Information
AI Technical Summary
Problems solved by technology
Method used
Image
Examples
Embodiment Construction
[0015] Such as figure 1 , figure 2 , image 3 As shown, the installation structure of the sound insulation wall of the railway vehicle machine room in this embodiment, the two sides of the sound insulation wall 1 are fully welded and connected with the corner column 2, the corner column 2 in this example adopts the angle iron with a section of 3X35X85mm, and the outer corner column 2 One side of the facade is fully welded to the side wall column 3, and the other side is connected to the side wall column 3 by section welding or dense spot welding; the lower beam 4 of the sound insulation wall is fully welded and connected with a patch 5, and the size of the patch is 2X120X3000mm, one side of the patch 5 is fully welded to the butt vertical plate 7 of the corrugated floor 6, and the other side of the patch 5 is welded to the crest of the corrugated floor 6; the upper end of the sound insulation wall 1 is fully welded to the 8 roof curved beams Solder connection.
[0016] It ...
PUM
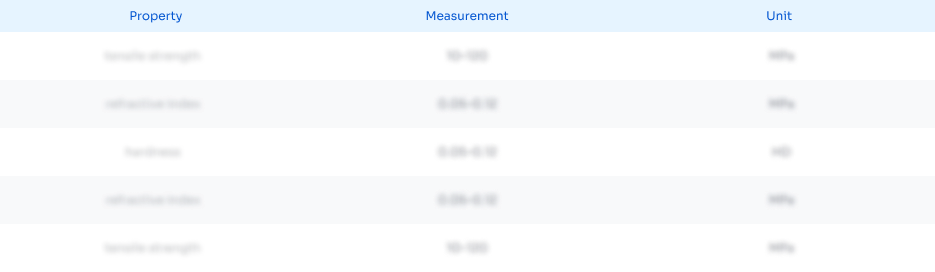
Abstract
Description
Claims
Application Information

- Generate Ideas
- Intellectual Property
- Life Sciences
- Materials
- Tech Scout
- Unparalleled Data Quality
- Higher Quality Content
- 60% Fewer Hallucinations
Browse by: Latest US Patents, China's latest patents, Technical Efficacy Thesaurus, Application Domain, Technology Topic, Popular Technical Reports.
© 2025 PatSnap. All rights reserved.Legal|Privacy policy|Modern Slavery Act Transparency Statement|Sitemap|About US| Contact US: help@patsnap.com