Method for preparing macromolecule ultrathin membrane nano wrinkling patterns
An ultra-thin film and polymer technology, which is applied in the field of preparing micro-nano scale patterns, can solve the problems of difficult shape maintenance, limited application, small swelling area, etc., and achieves the effect of improving simplicity and operability.
- Summary
- Abstract
- Description
- Claims
- Application Information
AI Technical Summary
Problems solved by technology
Method used
Image
Examples
Embodiment 1
[0032] First select polystyrene (PS) solvent toluene, then weigh a certain amount of polystyrene, and add a corresponding amount of toluene to make a 1wt% solution, then ultrasonic treatment accelerates the dissolution, and seal the reagent bottle for later use after dissolution is complete. The prepared solution was spin-coated to form a film, the spin-coating speed was 2000 rpm, the spin-coating time was 30s, and finally left for 24 hours to allow the solvent to evaporate completely. The spin-coated single-layer polymer film was treated with superthermal hydrogen technology to induce crosslinking on the upper layer of the polymer. The voltage of superthermal hydrogen was 300V and the treatment time was 2min. Then perform thermal annealing treatment, the annealing temperature is 130° C., and the annealing time is 6 hours. After annealing, take out the sample and allow it to cool rapidly to obtain a wrinkled pattern. wrinkle pattern as attached figure 1 shown.
Embodiment 2
[0034] First select polystyrene (PS) solvent toluene, then weigh a certain amount of polystyrene, and add a corresponding amount of toluene to make a 1wt% solution, then ultrasonic treatment accelerates the dissolution, and seal the reagent bottle for later use after dissolution is complete. The prepared solution is formed into a film by spin coating, and the substrate is a silicon wafer with grooves (see attached figure 2 ), the spin-coating speed is 2000 rpm, the spin-coating time is 30s, and finally placed for 24h to allow the solvent to evaporate completely. The spin-coated single-layer polymer film was treated with superthermal hydrogen technology to induce crosslinking on the upper layer of the polymer. The voltage of superthermal hydrogen was 300V and the treatment time was 2min. Then carry out thermal annealing treatment, the temperature of annealing is 130 ℃, the annealing time is 6h, after annealing, take out the sample and let it cool rapidly to get the wrinkle pat...
Embodiment 3
[0036]First select the solvent toluene of block polymer polystyrene isoprene triblock copolymer (SIS), yet weigh a certain amount of block polymer polystyrene isoprene triblock copolymer (SIS) , and add a corresponding amount of toluene to configure a 1wt% solution, and then ultrasonic treatment accelerates the dissolution. After the dissolution is complete, seal the reagent bottle for later use. The prepared solution was spin-coated to form a film, the spin-coating speed was 3000 rpm, the spin-coating time was 30s, and finally left for 24 hours to allow the solvent to evaporate completely. The spin-coated single-layer polymer film was treated with superthermal hydrogen technology to induce crosslinking on the upper layer of the polymer. The voltage of superthermal hydrogen was 300V and the treatment time was 5 minutes. Then carry out thermal annealing treatment, the temperature of annealing is 120 ℃, the annealing time is 6h, after annealing, take out the sample and let it co...
PUM
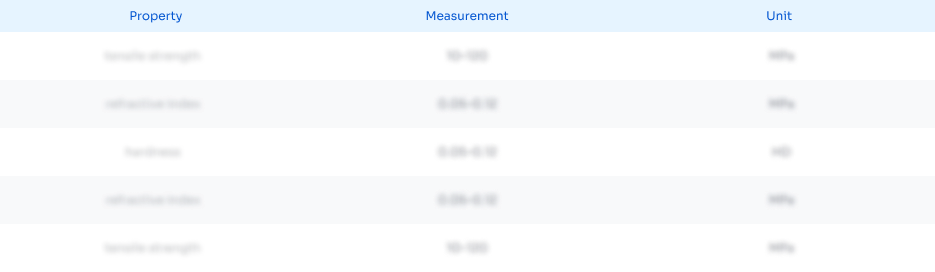
Abstract
Description
Claims
Application Information

- R&D
- Intellectual Property
- Life Sciences
- Materials
- Tech Scout
- Unparalleled Data Quality
- Higher Quality Content
- 60% Fewer Hallucinations
Browse by: Latest US Patents, China's latest patents, Technical Efficacy Thesaurus, Application Domain, Technology Topic, Popular Technical Reports.
© 2025 PatSnap. All rights reserved.Legal|Privacy policy|Modern Slavery Act Transparency Statement|Sitemap|About US| Contact US: help@patsnap.com