Process for heating carbon steel and low-alloy steel heavy piece-weight composite blank
A low-alloy steel and composite billet technology, which is applied in the field of metallurgical industry billet heating technology, can solve the problems of uneven heating of large single-weight composite billets, easy rolling cracking, etc., to reduce the risk of rolling cracking, reduce the degree of oxidation, The effect of reducing the soaking time
- Summary
- Abstract
- Description
- Claims
- Application Information
AI Technical Summary
Problems solved by technology
Method used
Image
Examples
Embodiment Construction
[0013] Such as figure 2 As shown, the heating process of a large single-weight composite billet of carbon steel and low alloy steel in the present invention includes three stages of preheating, heating and soaking, and a heat preservation process is added in the preheating and heating stages.
[0014] In the preheating stage, the composite bale is preheated to 580-620°C, and then kept at this temperature for 0.5-2h; the heating stage includes a heating stage I and a heating stage II, and in the heating stage I, the basil is Heating to 910°C, the heating rate is 100-130°C / h, and then keeping at this temperature for 0.5-2h; in the heating stage II, the ash material is heated to 1270°C, and the heating rate is 80-110°C / h.
[0015] In the heating process provided by the present invention, heat preservation is carried out at an appropriate temperature during the heating process, and the soaking time at high temperature is reduced. Compared with the traditional heating process, thi...
PUM
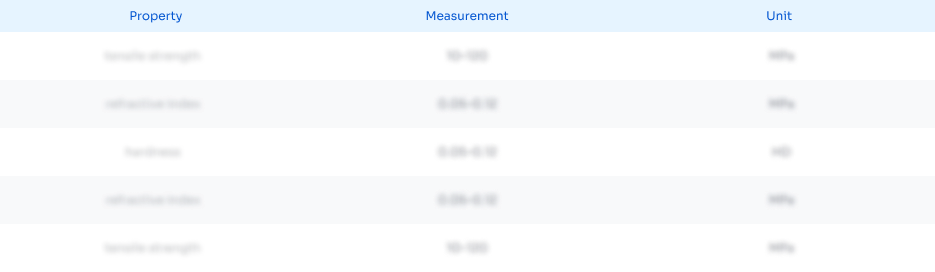
Abstract
Description
Claims
Application Information

- Generate Ideas
- Intellectual Property
- Life Sciences
- Materials
- Tech Scout
- Unparalleled Data Quality
- Higher Quality Content
- 60% Fewer Hallucinations
Browse by: Latest US Patents, China's latest patents, Technical Efficacy Thesaurus, Application Domain, Technology Topic, Popular Technical Reports.
© 2025 PatSnap. All rights reserved.Legal|Privacy policy|Modern Slavery Act Transparency Statement|Sitemap|About US| Contact US: help@patsnap.com