PVC (polyvinyl chloride) wood-like grain master batch and application thereof
A color masterbatch and imitation wood grain technology, which is applied in the field of plastic manufacturing, can solve the problems of "poor authenticity, high cost, and complicated molding process" of wood, and achieve the effect of realistic wood grain, good weather resistance, and clear lines of wood grain
- Summary
- Abstract
- Description
- Claims
- Application Information
AI Technical Summary
Problems solved by technology
Method used
Image
Examples
Embodiment 1
[0036] Prepare according to the parts by weight shown in each component in Table 1.
[0037] Table 1 The distribution ratio of each component of the masterbatch in Example 1 (parts by mass)
[0038] material name A component B component PVC SG-3 / 30 PVC SG-7 100 70 Calcium zinc stabilizer 5.0 5.5 Chlorinated polyethylene 8.0 7.0 light calcium carbonate 25.0 15 ACR-401 2.0 2.0 stearic acid 0.6 1.5 polyethylene wax 0.8 1.5 1010 0.4 0.6 UV531 0.2 0.3 carbon black 3.0 3.5 organic yellow 15.0 / organic red 7.0 / iron yellow / 9.0 Iron oxide red / 15.0
[0039] Preparation:
[0040] Step 1: Pour all the materials into a high-speed mixer according to the parts by weight of component A in the formula table and stir evenly. Stir the temperature to 100°C and discharge the materials into the hopper of the extruder. The materials are granulated by melt extrusion. Obt...
Embodiment 2
[0046] Embodiment 2 is prepared according to the parts by weight shown in each component in Table 2.
[0047] Table 2 The distribution ratio of each component of the color masterbatch in Example 2 (parts by mass)
[0048] material name A component B component PVC SG-1 / 20 PVC SG-5 100 80 Rare earth lead salt composite stabilizer 5.5 6.0 Chlorinated polyethylene 7.0 7.0 light calcium carbonate 5.0 30 ACR-401 1.5 1.5 MBS / 2.0 stearic acid 0.8 2.0 polyethylene wax 0.8 2.0 1010 0.4 0.6 UV531 0.2 0.3 carbon black 3.0 1.5 organic yellow 20 / organic red 5.0 / iron yellow / 5.0 Iron oxide red / 5.0
[0049] Preparation:
[0050] Step 1: Pour all the materials into a high-speed mixer according to the parts by weight of component A in the formula table and stir evenly. Stir the temperature to 100°C and discharge the materials into the hopper of the extruder...
Embodiment 3
[0056] Embodiment 3 is prepared according to the weight parts shown in each component of table 3
[0057] Table 3 The distribution ratio of each component of the masterbatch in Example 3 (parts by mass)
[0058] material name A component B component Polymer 2500—PVC / 15 PVC SG-5 100 85 Calcium zinc stabilizer 5.5 6.0 Chlorinated polyethylene 8.0 7.0 light calcium carbonate 5.0 8.0 MBS / 2.0 stearic acid 0.8 2.0 polyethylene wax 0.8 2.0 1010 0.4 0.6 UV531 0.2 0.3 carbon black 2.5 7.0 organic yellow 8 / organic red 4.0 / iron yellow / 5.0 Iron oxide red / 2.0
[0059] Preparation:
[0060] The first step is to pour all the materials into a high-speed mixer according to the weight of component A in the formula table and stir evenly. Stir the temperature to 100°C and discharge the material into the hopper of the extruder. The material is produced by melt extrusi...
PUM
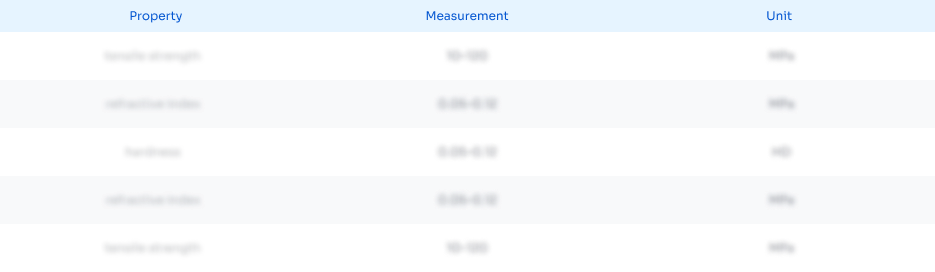
Abstract
Description
Claims
Application Information

- Generate Ideas
- Intellectual Property
- Life Sciences
- Materials
- Tech Scout
- Unparalleled Data Quality
- Higher Quality Content
- 60% Fewer Hallucinations
Browse by: Latest US Patents, China's latest patents, Technical Efficacy Thesaurus, Application Domain, Technology Topic, Popular Technical Reports.
© 2025 PatSnap. All rights reserved.Legal|Privacy policy|Modern Slavery Act Transparency Statement|Sitemap|About US| Contact US: help@patsnap.com