A polypropylene conductive plastic and a preparation method thereof
A conductive plastic, polypropylene technology, applied in the field of plastics, to achieve the effects of good mechanical properties, superior performance and stable performance
- Summary
- Abstract
- Description
- Claims
- Application Information
AI Technical Summary
Problems solved by technology
Method used
Examples
Embodiment 1
[0012] A polypropylene conductive plastic, comprising the following components in parts by weight: 40 parts of PP, 30 parts of carbon black, 20 parts of PP-g-MAH, 8 parts of ethylene-propylene rubber, 10 parts of aluminum powder (74um), tetrabutoxy 1 part of titanium base, 5 parts of dioctyl terephthalate, 5 parts of sodium sulfite, 10 parts of ammonium peroxodisulfate, 12 parts of diisobutyl phthalate, and 11 parts of isoeugenol.
[0013] The preparation method of the above-mentioned conductive plastic comprises the following steps: adding carbon black, PP-g-MAH, ethylene-propylene rubber, and aluminum powder to PP for mixing and melting, then sequentially adding tetrabutoxytitanium and isoeugenol, mixing, and finally Add dioctyl terephthalate, sodium sulfite, ammonium peroxodisulfate, and diisobutyl phthalate, and extrude the sheet at 220-225°C to obtain conductive plastic.
Embodiment 2
[0015] A polypropylene conductive plastic, including the following components in parts by weight: 50 parts of PP, 40 parts of carbon black, 25 parts of PP-g-MAH, 10 parts of ethylene-propylene rubber, 15 parts of aluminum powder (150um), tetrabutoxide 15 parts of titanium base, 9 parts of dioctyl terephthalate, 6 parts of sodium sulfite, 19 parts of ammonium peroxodisulfate, 18 parts of diisobutyl phthalate, and 17 parts of isoeugenol.
[0016] The preparation method of the above-mentioned conductive plastic comprises the following steps: adding carbon black, PP-g-MAH, ethylene-propylene rubber, and aluminum powder to PP for mixing and melting, then sequentially adding tetrabutoxytitanium and isoeugenol, mixing, and finally Add dioctyl terephthalate, sodium sulfite, ammonium peroxodisulfate, and diisobutyl phthalate, and extrude the sheet at 220-225°C to obtain conductive plastic.
Embodiment 3
[0018] A polypropylene conductive plastic, comprising the following components in parts by weight: 45 parts of PP, 32 parts of carbon black, 22 parts of PP-g-MAH, 9 parts of ethylene-propylene rubber, 13 parts of aluminum powder (10um), tetrabutoxy 10 parts of titanium base, 7 parts of dioctyl terephthalate, 5.5 parts of sodium sulfite, 12 parts of ammonium peroxodisulfate, 13 parts of diisobutyl phthalate, and 14 parts of isoeugenol.
[0019] The preparation method of the above-mentioned conductive plastic comprises the following steps: adding carbon black, PP-g-MAH, ethylene-propylene rubber, and aluminum powder to PP for mixing and melting, then sequentially adding tetrabutoxytitanium and isoeugenol, mixing, and finally Add dioctyl terephthalate, sodium sulfite, ammonium peroxodisulfate, and diisobutyl phthalate, and extrude the sheet at 220-225°C to obtain conductive plastic.
[0020] Below by the performance of the product that test test embodiment 1,2,3 makes:
...
PUM
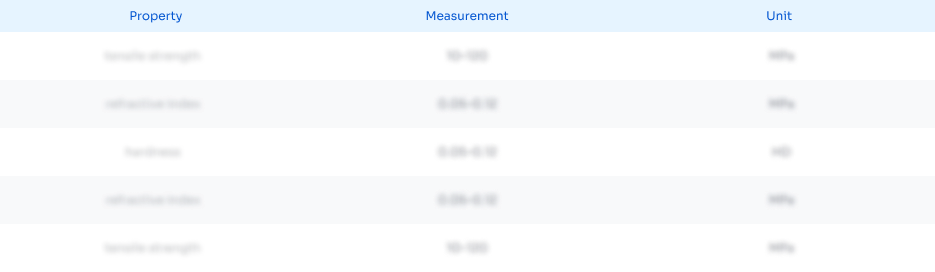
Abstract
Description
Claims
Application Information

- Generate Ideas
- Intellectual Property
- Life Sciences
- Materials
- Tech Scout
- Unparalleled Data Quality
- Higher Quality Content
- 60% Fewer Hallucinations
Browse by: Latest US Patents, China's latest patents, Technical Efficacy Thesaurus, Application Domain, Technology Topic, Popular Technical Reports.
© 2025 PatSnap. All rights reserved.Legal|Privacy policy|Modern Slavery Act Transparency Statement|Sitemap|About US| Contact US: help@patsnap.com