Method for casting cast broken wall and rolling mortar wall evaporated pattern
A production method and technology of lost foam, applied in the field of casting modeling, can solve the problems of immature casting, many casting defects, large gas generation, etc., and achieve the effect of improving quality, stability and quality
- Summary
- Abstract
- Description
- Claims
- Application Information
AI Technical Summary
Problems solved by technology
Method used
Image
Examples
Embodiment 1
[0029] SJ1400 broken wall lost foam production
[0030] Foam 3kg of polystyrene in a foaming machine, the temperature is controlled at 90-100°C, the air pressure is controlled at 0.6-0.8MPa, the time is 5 minutes, the specific gravity of the foam is 17g / liter; the foam is left to stand in the air for 8-10 Hours, then molded with a foam molding machine, the temperature is controlled at 100-110°C, the air pressure is controlled at 0.6-0.8MPa, and the time is 10 minutes. One-time molding is made into the lost foam of the casting broken wall, and finally the lost foam is dried. The temperature is 35-40℃, and the drying time is 24-30 hours. The manufactured SJ1400 broken wall lost foam has an upper diameter of 1300mm and a lower diameter of 307mm.
Embodiment 2
[0032] SJ1400 Rolling Mortar Wall Lost Foam Fabrication
[0033] Foam 3.5kg of polystyrene in a foaming machine, the temperature is controlled at 90-100°C, the air pressure is controlled at 0.6-0.8MPa, the time is 5 minutes, and the specific gravity of the foam is 17g / liter; the foam is left to stand in the air for 8- After 10 hours, use a foam molding machine to form, the temperature is controlled at 100-110°C, the air pressure is controlled at 0.6-0.8MPa, and the time is 11 minutes. The lost foam of the casting rolling wall is formed at one time, and finally the lost foam is dried. The drying temperature is 35-40°C, and the drying time is 30-36 hours. The manufactured SJ1400 broken wall lost foam has an upper diameter of 1409mm and a lower diameter of 814mm.
Embodiment 3
[0035] SJ1650 broken wall lost foam production
[0036] Foam 4kg of polystyrene in a foaming machine, the temperature is controlled at 90-100°C, the air pressure is controlled at 0.6-0.8MPa, the time is 5 minutes, the specific gravity of the foam is 18g / liter; the foam is left to stand in the air for 8-10 Hours, and then molded with a foam molding machine, the temperature is controlled at 100-110°C, the air pressure is controlled at 0.6-0.8MPa, and the time is 12 minutes. One-time molding is made into the lost foam of the casting broken wall, and finally the lost foam is dried. The temperature is 35-40℃, and the drying time is 24-36 hours. The manufactured SJ1400 broken wall lost foam has an upper diameter of 381.3mm and a lower diameter of 1563mm.
PUM
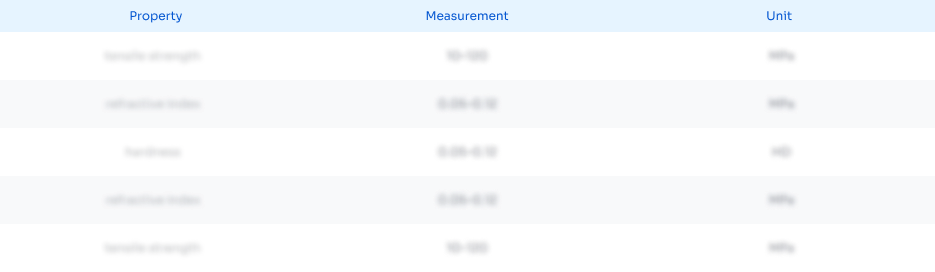
Abstract
Description
Claims
Application Information

- R&D
- Intellectual Property
- Life Sciences
- Materials
- Tech Scout
- Unparalleled Data Quality
- Higher Quality Content
- 60% Fewer Hallucinations
Browse by: Latest US Patents, China's latest patents, Technical Efficacy Thesaurus, Application Domain, Technology Topic, Popular Technical Reports.
© 2025 PatSnap. All rights reserved.Legal|Privacy policy|Modern Slavery Act Transparency Statement|Sitemap|About US| Contact US: help@patsnap.com