Seal rubber used for valves and preparation method thereof
A technology for sealing rubber and valves, applied in the field of valve sealing, can solve problems such as affecting the appearance quality and reducing the use performance, and achieve the effect of improving tear resistance and solving frost spraying.
- Summary
- Abstract
- Description
- Claims
- Application Information
AI Technical Summary
Problems solved by technology
Method used
Examples
Embodiment 1
[0022] A. Put 1,000 grams of broken nitrile rubber NBR2845 into the rolls for mastication; masticate until the nitrile rubber is completely covered with rolls and there is no cracked opening.
[0023] B. Slowly add anti-aging agent BLE, 20 grams, anti-aging agent 4020, 20 grams, anti-aging agent DNP, 5 grams, to the raw rubber in step A, pound and mix evenly, and the color of the rubber material is uniform when cutting the bread roll. .
[0024] C. Add 50 grams of zinc oxide ZnO and 5 grams of sulfur S to the raw glue of step B respectively, and pound until evenly distributed.
[0025] D, add stearic acid SA, 10 grams, and carbon black N220, 200 grams, white carbon black, 133 grams, wherein 400 mesh white carbon black 33 grams and 800 mesh white carbon black 100 grams; On the raw material of step C, ramming to an even distribution.
[0026] E. Add 400 grams of remaining carbon black, softener DOP, 200 grams to the raw material in step D in 5 times, after grinding into the ru...
Embodiment 2
[0030] A. Put 1200 grams of the broken nitrile rubber NBR2845 into the rolls for mastication; masticate until the nitrile rubber is completely covered with the rolls without cracked openings.
[0031] B. Slowly add anti-aging agent BLE, 30 grams, anti-aging agent 4020, 30 grams, anti-aging agent DNP, 20 grams, to the raw rubber of step A, pound and mix evenly, and the color of the rubber material is uniform when cutting the bread roll. .
[0032] C. Add 70 grams of zinc oxide ZnO and 25 grams of sulfur S to the raw glue of step B respectively, and ram until they are evenly distributed.
[0033] D, add stearic acid SA, 30 grams, and carbon black N220, 250 grams, white carbon black, 150 grams, on the raw material of step C, ramming until uniform distribution.
[0034] E. Add 550 grams of remaining carbon black, softener DOP, and 400 grams to the raw materials in step D in 6 times. After grinding into the rubber material, cut the rubber surface to make the raw materials evenly d...
Embodiment 3
[0038] A. Put the broken nitrile rubber NBR2845, 800 grams into the rolls for mastication; masticate until the nitrile rubber is completely covered with the rolls without cracked openings.
[0039] B. Slowly add anti-aging agent BLE, 10 grams, anti-aging agent 4020, 10 grams, anti-aging agent DNP, 2 grams, to the raw rubber in step A, pound and mix evenly, and the color of the rubber material is uniform when cutting the bread roll. .
[0040] C. Add 30 grams of zinc oxide ZnO and 2 grams of sulfur S to the raw glue of step B successively, and pound until evenly distributed.
[0041] D, add stearic acid SA, 5 grams, and carbon black N220, 130 grams, white carbon black, 100 grams, wherein 400 mesh white carbon black 25 grams and 800 mesh white carbon black 75 grams; On the raw material of step C, ramming to an even distribution.
[0042] E. Add 270 grams of remaining carbon black, softener DOP, and 20 grams to the raw materials in step D in 4 times. After grinding into the rub...
PUM
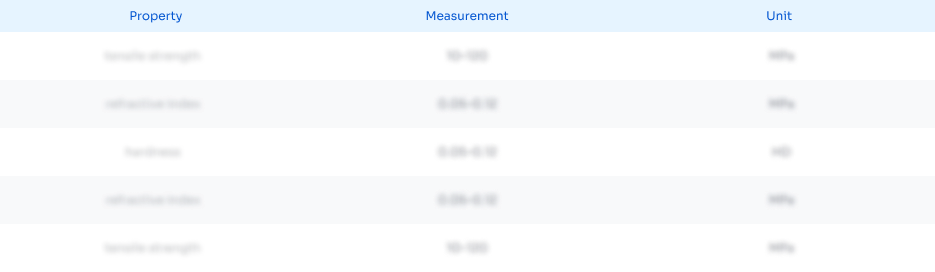
Abstract
Description
Claims
Application Information

- R&D Engineer
- R&D Manager
- IP Professional
- Industry Leading Data Capabilities
- Powerful AI technology
- Patent DNA Extraction
Browse by: Latest US Patents, China's latest patents, Technical Efficacy Thesaurus, Application Domain, Technology Topic, Popular Technical Reports.
© 2024 PatSnap. All rights reserved.Legal|Privacy policy|Modern Slavery Act Transparency Statement|Sitemap|About US| Contact US: help@patsnap.com