Process and device for preparing superfine nickel powder
A process and technology of nickel powder, which is applied in the field of ultrafine powder preparation, can solve problems such as cohesive flow loss, low purity of ultrafine nickel powder, and poor fluidity of ultrafine nickel powder, so as to prevent flow loss and improve heat utilization High, uniform and rapid fluidization effect
- Summary
- Abstract
- Description
- Claims
- Application Information
AI Technical Summary
Problems solved by technology
Method used
Image
Examples
Embodiment 1
[0056] Ultrafine nickel oxide (particle size smaller than 2 The volume concentration is 50%, and the contact mode is countercurrent, so that the material is in a state of bubbling fluidization. The residence time of the materials in the first fluidized bed reactor 5 is 15 minutes, so that the conversion rate of nickel oxide after the reaction in the first fluidized bed reactor is about 80%; then it is sent to the second through the second feed valve 6 Fluidized bed reactor 7; the tail gas is discharged through the outlet of the first cyclone 11, and enters the burner of the combustion chamber 15 to produce high-temperature hot flue gas. The high-temperature flue gas discharged from the outlet of the combustion chamber 15 enters the cyclone preheater 3 and superfine After the nickel oxide powder undergoes heat exchange, the entrained fine powder is removed by the cyclone 16 and the bag filter 17 and then vented; the reaction temperature of the second fluidized bed reactor 7 is 60...
Embodiment 2
[0059] Ultrafine nickel oxide (particle size smaller than 2 The volume concentration is 30%, and the contact mode is countercurrent, so that the material is in a state of bubbling fluidization. The residence time of the material in the first fluidized bed reactor 5 is 10 minutes, so that the conversion rate of nickel oxide after the reaction in the first fluidized bed reactor is about 80%; then it is sent to the second through the second feed valve 6 Fluidized bed reactor 7; tail gas is discharged through the outlet of the first cyclone 11, and enters the burner of the combustion chamber 15 to produce high-temperature hot flue gas. The high-temperature flue gas discharged from the outlet of the combustion chamber 15 enters the cyclone preheater 3 and superfine After the nickel oxide powder undergoes heat exchange, the entrained fine powder is removed by the cyclone 16 and the bag filter 17 and then vented; the reaction temperature of the second fluidized bed reactor 7 is 500°C, ...
Embodiment 3
[0062] The ultrafine nickel oxide (particle size smaller than the 2 The volume concentration is 60%, and the contact mode is cross flow, so that the material is in a state of bubbling fluidization. The residence time of the material in the first fluidized bed reactor 5 is 5 minutes, so that the conversion rate of nickel oxide after the reaction in the first fluidized bed reactor 5 is about 80%; then it is sent to the second feed valve 6 through the second feed valve 6 Two fluidized bed reactor 7; the tail gas is discharged through the outlet of the first cyclone separator 11, and enters the burner of the combustion chamber 15 to produce high-temperature hot flue gas. The high-temperature flue gas discharged from the outlet of the combustion chamber 15 enters the cyclone preheater 3 and super After the fine nickel oxide powder undergoes heat exchange, the entrained fine powder is removed by the cyclone 16 and the bag filter 17 and then vented; the reaction temperature of the seco...
PUM
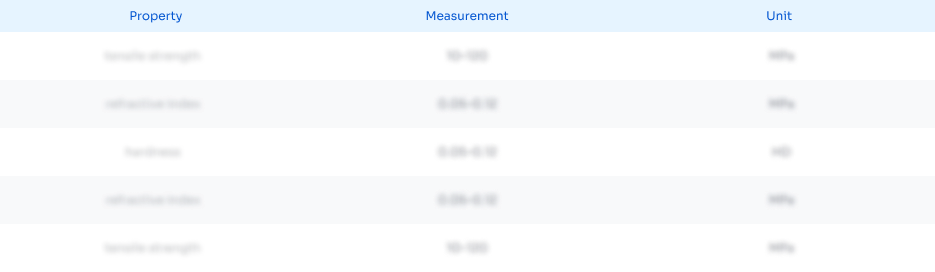
Abstract
Description
Claims
Application Information

- R&D
- Intellectual Property
- Life Sciences
- Materials
- Tech Scout
- Unparalleled Data Quality
- Higher Quality Content
- 60% Fewer Hallucinations
Browse by: Latest US Patents, China's latest patents, Technical Efficacy Thesaurus, Application Domain, Technology Topic, Popular Technical Reports.
© 2025 PatSnap. All rights reserved.Legal|Privacy policy|Modern Slavery Act Transparency Statement|Sitemap|About US| Contact US: help@patsnap.com