Permanent violet alkylating process
An alkylation and permanent violet technology, applied in organic dyes and other directions, can solve the problems of large manpower, material resources and energy consumption, cumbersome processes, and increased occupational hazard risks, saving manpower, reducing processes, and reducing occupational hazards. Effect
- Summary
- Abstract
- Description
- Claims
- Application Information
AI Technical Summary
Problems solved by technology
Method used
Examples
Embodiment 1
[0014] The permanent violet alkylation process of the present invention comprises the following steps: 600g of liquid caustic soda, 100g of carbazole, 5g of polyethylene glycol, and 75.06g of partial bromoethane are dropped into three ports of a stirring and reflux condenser with a concentration of 30%. In the flask, slowly heat up to 35°C, drop the remaining 35g of ethyl bromide at this temperature, after the dropwise addition, continue to heat up with the reaction, keep the temperature below the boiling point of the system, and when the conversion rate of carbazole reaches 99.5% The above is regarded as the end of the reaction, stand still for 10 minutes, remove the lower layer of liquid alkali and apply mechanically to obtain molten N-ethylcarbazole.
Embodiment 2
[0016] The permanent violet alkylation process of the present invention comprises the following steps: 400g of liquid caustic soda, carbazole 100g, polyethylene glycol 2.18g, benzyltriethylammonium chloride 0.55g, ethanol 0.27g with a concentration of 40% 1. Put 71.80g of bromoethane into a three-necked flask with stirring and reflux condenser, heat slowly to 35°C, add the remaining 38.2g of bromoethane dropwise at this temperature, after the dropwise addition, continue to heat up with the reaction , the control temperature is always lower than the boiling point of the system. When the conversion rate of carbazole reaches more than 99.5%, the reaction is considered to be over, and it is left to stand for 20 minutes.
Embodiment 3
[0018] The permanent violet alkylation process of the present invention comprises the following steps: 300g of liquid caustic soda, 100g of carbazole, 0.83g of polyethylene glycol, 0.83g of benzyltriethylammonium chloride, and 0.34g of ethanol with a concentration of 40% 1. Put 68.53g of ethyl bromide into a three-necked flask with stirring and reflux condenser, heat slowly to 35-40°C, add the remaining 45.47g of ethyl bromide dropwise at this temperature, after the dropwise addition, proceed with the reaction Constantly raise the temperature and control the temperature to be lower than the boiling point of the system. When the conversion rate of carbazole reaches 99.5% or more, the reaction is considered to be over. After standing still for 30 minutes, the lower layer of liquid alkali is separated and applied mechanically to obtain molten N-ethyl carbazole.
PUM
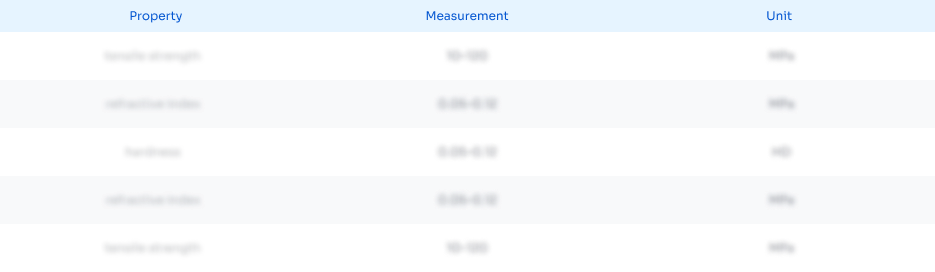
Abstract
Description
Claims
Application Information

- R&D Engineer
- R&D Manager
- IP Professional
- Industry Leading Data Capabilities
- Powerful AI technology
- Patent DNA Extraction
Browse by: Latest US Patents, China's latest patents, Technical Efficacy Thesaurus, Application Domain, Technology Topic, Popular Technical Reports.
© 2024 PatSnap. All rights reserved.Legal|Privacy policy|Modern Slavery Act Transparency Statement|Sitemap|About US| Contact US: help@patsnap.com