Thermal compression bonding power source
A technology of hot pressing welding and hot pressing welding head, applied in the field of hot pressing welding, can solve the problems of control error, large fluctuation of temperature control waveform, temperature overshoot, etc., and achieve the effect of improving stability and avoiding temperature overshoot.
- Summary
- Abstract
- Description
- Claims
- Application Information
AI Technical Summary
Problems solved by technology
Method used
Image
Examples
Embodiment Construction
[0031] The specific implementation of the heat-compression welding power source of the present invention will be described in detail below in conjunction with the accompanying drawings.
[0032] figure 2 It shows a schematic structural diagram of a thermocompression welding power source of an embodiment, including: a main circuit for outputting direct current / pulse current to a thermocompression welding head, a controller, and current sampling circuits respectively connected to the thermocompression welding heads , voltage sampling circuit and temperature detection circuit.
[0033] The main circuit adjusts the output current of the main circuit according to the PWM signal output by the controller.
[0034] The current sampling circuit collects the output current of the main circuit to obtain a feedback current value and outputs it to the controller.
[0035] The voltage sampling circuit collects the voltage at both ends of the thermocompression welding head to obtain a fee...
PUM
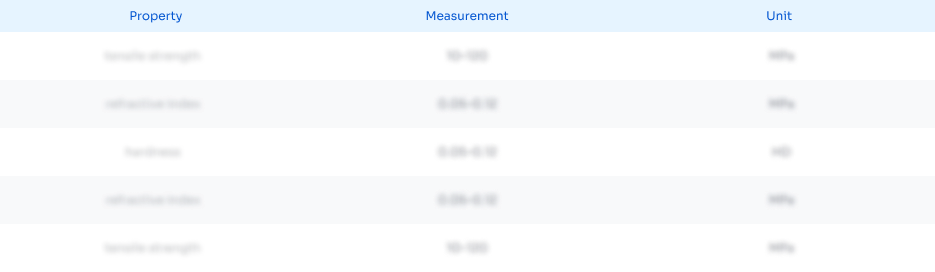
Abstract
Description
Claims
Application Information

- Generate Ideas
- Intellectual Property
- Life Sciences
- Materials
- Tech Scout
- Unparalleled Data Quality
- Higher Quality Content
- 60% Fewer Hallucinations
Browse by: Latest US Patents, China's latest patents, Technical Efficacy Thesaurus, Application Domain, Technology Topic, Popular Technical Reports.
© 2025 PatSnap. All rights reserved.Legal|Privacy policy|Modern Slavery Act Transparency Statement|Sitemap|About US| Contact US: help@patsnap.com