Combustion control method for regenerative pulse heating furnace
A technology of pulse heating and control method, which is applied in the field of metallurgical production and can solve problems such as product performance fluctuations, unevenness, and overtemperature
- Summary
- Abstract
- Description
- Claims
- Application Information
AI Technical Summary
Problems solved by technology
Method used
Image
Examples
no. 1 example
[0094] The initial state of the lower section of the soaking section is that all 4 pairs of regenerative burners are working. Due to the change of rolling line rhythm, the heat demand is reduced. The technology of this patent is used for regenerative pulse combustion control:
[0095] First determine the regenerative pulse combustion control gear. According to the MV value 1497 (flow setting value) of the lower part of the soaking section obtained, and the maximum flow value 3742 at the bottom of the soaking section of the flow classification threshold value table, calculate the flow percentage=1497 / 3742=40%, this value and the classification The grade range values in the threshold table are compared one by one to determine the current grade Lnew=3, thus also confirming that three pairs of burners need to be opened under this flow grade.
[0096] Then calculate the exhaust gas temperature curve. Using the heat storage box model, according to the parameters of the heat stora...
no. 2 example
[0101] The initial state of the lower part of the soaking section is that 3 pairs of regenerative burners are working. Due to the roll change of the rolling line, the heat demand is reduced. The technology of this patent is used to control the regenerative pulse combustion:
[0102] First determine the regenerative pulse combustion control gear. According to the MV value 1122 (flow setting value) of the lower part of the soaking section obtained, and the maximum flow value 3742 of the lower section of the soaking section of the flow classification threshold value table, the calculation flow percentage=1122 / 3742=30%, this value and the classification The values in the threshold table are compared one by one to determine the current gear level Lnew=2, thereby also determining that two pairs of burners need to be opened under this flow level.
[0103] Then calculate the exhaust gas temperature curve. Using the heat storage box model, according to the parameters of the heat sto...
no. 3 example
[0108] The initial state of the lower section of the soaking section is that 2 pairs of regenerative burners are working. Due to the failure of the rolling line, the heat demand is reduced. The technology of this patent is used to control the regenerative pulse combustion:
[0109] First determine the regenerative pulse combustion control gear. According to the MV value 561 (flow setting value) at the bottom of the soaking section obtained, and the maximum flow value 3742 at the bottom of the soaking section of the flow classification threshold table, calculate the flow percentage=561 / 3742=15%, this value and the classification threshold The values in the table are compared one by one to determine the current gear level Lnew=1, thereby also determining that a pair of burners need to be opened under this flow level.
[0110]Then calculate the exhaust gas temperature curve. Using the heat storage box model, according to the parameters of the heat storage pellets, the superfic...
PUM
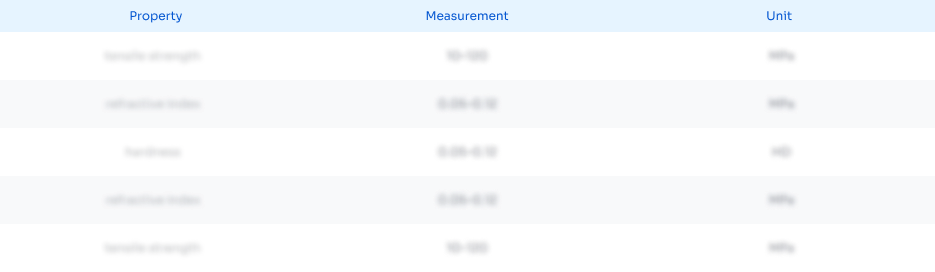
Abstract
Description
Claims
Application Information

- R&D
- Intellectual Property
- Life Sciences
- Materials
- Tech Scout
- Unparalleled Data Quality
- Higher Quality Content
- 60% Fewer Hallucinations
Browse by: Latest US Patents, China's latest patents, Technical Efficacy Thesaurus, Application Domain, Technology Topic, Popular Technical Reports.
© 2025 PatSnap. All rights reserved.Legal|Privacy policy|Modern Slavery Act Transparency Statement|Sitemap|About US| Contact US: help@patsnap.com