Carboxyethyl chitosan fiber and preparation method thereof
The technology of chitosan fiber and carboxyethyl group is applied in the field of fiber material preparation, which can solve the problems of uncertain distribution position and quantity of substituents, difficult to effectively control the liquid absorption performance of the product, and no antibacterial property, etc., so as to reduce pain, Inhibition of bacterial growth on wound surfaces and increased effects of polycationic properties
- Summary
- Abstract
- Description
- Claims
- Application Information
AI Technical Summary
Problems solved by technology
Method used
Image
Examples
preparation example Construction
[0031] The preparation method of carboxyethyl chitosan fiber, described preparation method is carried out as follows:
[0032] a. Disperse chitosan fiber in alcohol, the mass volume ratio of chitosan fiber to alcohol is 1:10~50, then add acrylic acid to the mixture of chitosan fiber and alcohol, the amino group of acrylic acid and chitosan fiber The molar ratio is 1:0.1~20, stir evenly at room temperature, and react in a constant temperature water bath at 40~90°C for 4~48h; the alcohol is one of methanol, ethanol, propanol, butanol or isopropanol .
[0033] Generally speaking, chitosan is difficult to form polycations under neutral or alkaline conditions, and the antibacterial effect is weak. The present invention is through the Michael addition reaction of the amino group on the molecular chain of chitosan and the carbon-carbon double bond on the acrylic acid molecule. A carboxyethyl group is introduced on the N position. The carboxylic acid on the carboxyethyl group gives ...
Embodiment 1
[0042]Weigh 5 g of chitosan fibers and disperse them in 50 mL of methanol, add 22.38 g of acrylic acid, shake and stir at room temperature, react in a constant temperature water bath at 90°C for 48 hours, separate the reacted chitosan fibers from the reaction mixture, and separate The chitosan fibers produced were dispersed in 80% (v / v) methanol aqueous solution, and 30% (w / v) sodium hydroxide aqueous solution was added dropwise, the pH of methanol and sodium hydroxide aqueous solution mixture was adjusted to 7.3, soaked for 30 minutes, Then the soaked chitosan fibers were separated from the mixture, washed twice with 80% (v / v) methanol aqueous solution, dehydrated, and dried at 40°C to obtain 0.8 carboxyethyl chitosan fiber.
Embodiment 2
[0044] Weigh 5 g of chitosan fibers and disperse them in 250 mL of ethanol, add 0.11 g of acrylic acid, shake and stir at room temperature, react in a constant temperature water bath at 40°C for 4 hours, separate the reacted chitosan fibers from the reaction mixture, and separate The obtained chitosan fibers were dispersed in 80% (v / v) ethanol aqueous solution, and 30% (w / v) potassium hydroxide aqueous solution was added dropwise, and the pH of the mixture of ethanol and potassium hydroxide aqueous solution was adjusted to 8.0, soaked for 30 minutes, Then the soaked chitosan fiber is separated from the mixture, washed twice with 80% (v / v) ethanol aqueous solution, dehydrated, and dried at 40°C to obtain a fiber with a viscosity of 900 cps and a carboxyethyl substitution degree 0.01 carboxyethyl chitosan fiber.
PUM
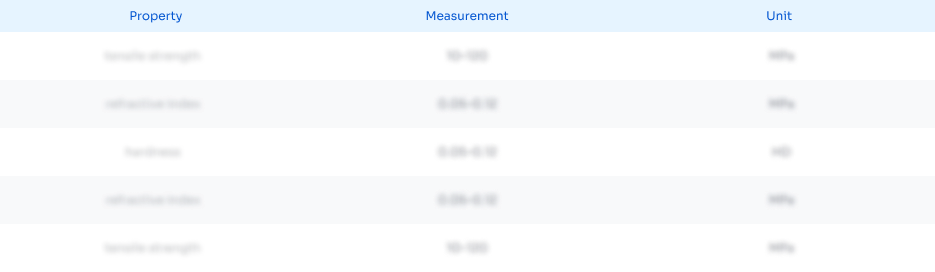
Abstract
Description
Claims
Application Information

- Generate Ideas
- Intellectual Property
- Life Sciences
- Materials
- Tech Scout
- Unparalleled Data Quality
- Higher Quality Content
- 60% Fewer Hallucinations
Browse by: Latest US Patents, China's latest patents, Technical Efficacy Thesaurus, Application Domain, Technology Topic, Popular Technical Reports.
© 2025 PatSnap. All rights reserved.Legal|Privacy policy|Modern Slavery Act Transparency Statement|Sitemap|About US| Contact US: help@patsnap.com