Method for preparing low-carbon stainless steel
A stainless steel and molten steel technology, applied in the field of manufacturing low-carbon stainless steel, can solve the problems of low decarburization efficiency and poor decarburization conditions, and achieve high decarburization efficiency and thorough decarburization
- Summary
- Abstract
- Description
- Claims
- Application Information
AI Technical Summary
Problems solved by technology
Method used
Examples
Embodiment 1
[0063] Ⅰ Pretreatment of hot metal
[0064] 73 tons of molten iron of the mass percentage of following composition are carried out pretreatment:
[0065] S 0.038%; P 0.087%; Si 0.36%; the rest is Fe and unavoidable impurities. The temperature of molten iron is 1320°C.
[0066] After the molten iron is pretreated by removing S, P and Si, the mass percentage of the composition of the molten iron meets the following requirements:
[0067] S 0.022%; P 0.005%; Si 0.03%; the rest is Fe and unavoidable impurities, and the temperature of molten iron after pretreatment is 1290°C.
[0068] Ⅱ K-OBM-S converter smelting
[0069] The pretreated molten iron is added to the K-OBM-S converter for smelting, and the converter is bottom-blown with N 2 Gas operation, adding lime to each ton of molten iron—100kg / t, lightly burned magnesium balls—25kg / t, coke—18kg / t, high-carbon ferrochrome (69.2% chromium)-25 kg / t, high-carbon ferromanganese ( 7.5% carbon, 76% manganese)-3.5 kg / t...
Embodiment 2
[0100] Ⅰ Pretreatment of hot metal
[0101] 75 tons of molten iron of the mass percentage of following composition is carried out pretreatment:
[0102] S 0.028%; P 0.073%; Si 0.034%;
[0103] The rest is Fe and unavoidable impurities, and the temperature of molten iron is 1290°C.
[0104] After the molten iron is pretreated by removing S, P and Si, the mass percentage of the composition of the molten iron meets the following requirements:
[0105] S 0.015%; P 0.004%; Si 0.025%; the rest is Fe and unavoidable impurities, and the temperature of molten iron after pretreatment is 1270°C.
[0106] Ⅱ K-OBM-S converter smelting
[0107] The pretreated molten iron is added to the K-OBM-S converter for smelting, and the converter is bottom-blown with N 2 gas operation,
[0108] Add lime to each ton of molten iron—100kg / t, lightly burned magnesium balls—25kg / t, coke—18kg / t, high-carbon ferrochromium (69.2% chromium)-25 kg / t, high-carbon ferromanganese (carbon 7.5 %,...
PUM
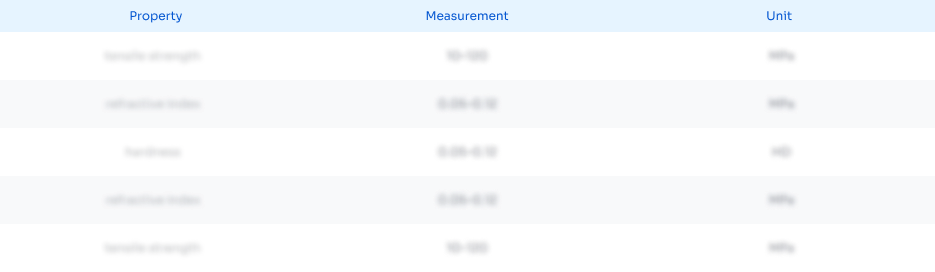
Abstract
Description
Claims
Application Information

- R&D
- Intellectual Property
- Life Sciences
- Materials
- Tech Scout
- Unparalleled Data Quality
- Higher Quality Content
- 60% Fewer Hallucinations
Browse by: Latest US Patents, China's latest patents, Technical Efficacy Thesaurus, Application Domain, Technology Topic, Popular Technical Reports.
© 2025 PatSnap. All rights reserved.Legal|Privacy policy|Modern Slavery Act Transparency Statement|Sitemap|About US| Contact US: help@patsnap.com