Fiber cement composite plate production process
A technology of fiber cement and production process, which is applied in the field of building boards, can solve the problems of poor fire resistance, poor waterproofness, and low strength, and achieve the effects of improved heat resistance, excellent waterproof performance, and low thermal conductivity
- Summary
- Abstract
- Description
- Claims
- Application Information
AI Technical Summary
Problems solved by technology
Method used
Image
Examples
Embodiment 1
[0070] The production process of the fiber cement composite board provided in this embodiment, the fiber cement composite board includes middle material, glass fiber cloth and bottom material,
[0071] The base material includes Portland cement, water and chemical additives, wherein the weight content of each component is: Portland cement: 50 parts; water: 35 parts; air-entraining agent: 2 parts; waterproofing agent: 5 parts; Water agent: 5 parts; add the above water and chemical additives into the mixer and pre-mix for 60 seconds, then add Portland cement and mix evenly for later use;
[0072] The middle material includes Portland cement, water, river sand, wood chaff and ceramsite, wherein the weight content of each component is: Portland cement: 500 parts; water: 350 parts; river sand: 140 parts; ceramsite : 120 parts; wood bran: 75 parts; air-entraining agent: 4 parts; waterproofing agent: 7 parts; Add to a blender and stir evenly for later use;
[0073] First, the stirr...
Embodiment 2
[0077] This embodiment provides a kind of production process of fiber cement composite board, fiber cement composite board comprises middle material, glass fiber cloth and base material,
[0078] The base material includes Portland cement, water and chemical additives, wherein the weight content of each component is: Portland cement: 60 parts; water: 50 parts; air-entraining agent: 5 parts; waterproofing agent: 8 parts; Water agent: 8 parts; add the above water and chemical additives into the mixer and pre-mix for 90 seconds, then add Portland cement and mix evenly for later use;
[0079] The middle material includes Portland cement, water, river sand, wood chaff and ceramsite, wherein the weight content of each component is: Portland cement: 550 parts; water: 400 parts; river sand: 150 parts; ceramsite : 150 parts; wood bran: 90 parts; air-entraining agent: 5 parts; waterproofing agent: 10 parts; Add to a blender and stir evenly for later use;
[0080] First, the stirred bo...
Embodiment 3
[0084] The production process of the fiber cement composite board provided in this embodiment, the fiber cement composite board includes middle material, glass fiber cloth and bottom material,
[0085] The base material includes Portland cement, water and chemical additives, wherein the weight content of each component is: Portland cement: 40 parts; water: 25 parts; air-entraining agent: 1 part; waterproofing agent: 3 parts; Water agent: 3 parts; add the above water and chemical additives to the mixer and pre-mix for 40 seconds, then add Portland cement and mix evenly for later use;
[0086] The medium material includes Portland cement, water, river sand, wood chaff and ceramsite, wherein the weight content of each component is: Portland cement: 480 parts; water: 300 parts; river sand: 100 parts; ceramsite : 100 parts; wood bran: 60 parts; air-entraining agent: 5 parts; waterproofing agent: 10 parts; Add to a blender and stir evenly for later use;
[0087] First, the stirred...
PUM
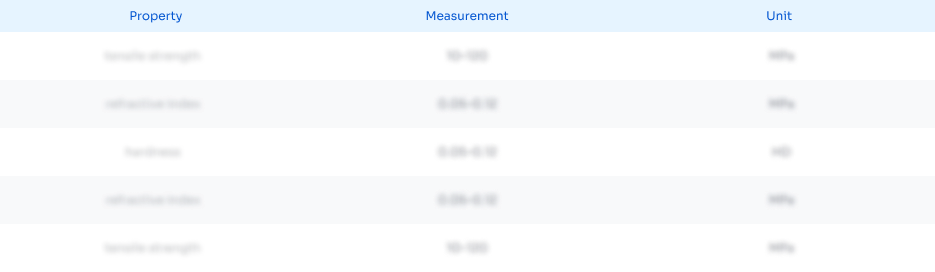
Abstract
Description
Claims
Application Information

- R&D
- Intellectual Property
- Life Sciences
- Materials
- Tech Scout
- Unparalleled Data Quality
- Higher Quality Content
- 60% Fewer Hallucinations
Browse by: Latest US Patents, China's latest patents, Technical Efficacy Thesaurus, Application Domain, Technology Topic, Popular Technical Reports.
© 2025 PatSnap. All rights reserved.Legal|Privacy policy|Modern Slavery Act Transparency Statement|Sitemap|About US| Contact US: help@patsnap.com