Abrasion-resistant zone welding powder
A technology of welding powder and wear-resistant layer, which is applied in the field of surface treatment materials and welding materials, can solve the problems of high brittleness of hard phase, pressure drop in the well, easy peeling of wear-resistant belt, etc., and achieve high surface hardness, low friction coefficient, The effect of not easy to peel off
- Summary
- Abstract
- Description
- Claims
- Application Information
AI Technical Summary
Problems solved by technology
Method used
Image
Examples
Embodiment 1
[0013] The grinding layer solder powder provided by the best embodiment 1 of the present invention comprises the following components by weight percentage:
[0014] Chromium: 4-15%; Nickel: 3-10%; Manganese: 0.2-2%; Vanadium: 1-3%; Silicon: 1-5%; Rare Earth: 0.5-2%; Carbon: 1-5%; The amount is iron and trace impurities.
[0015] The above-mentioned solder powder is mixed with ferrochrome (FeCr57) block, nickel block, ferromanganese (FeMn75) block, vanadium iron (FeV50) block, metal silicon block, rare earth particles, carbon particles and iron block in a certain weight ratio and then melted, It is obtained by dusting, drying and sieving.
[0016] Such as figure 1 As shown, ferrochromium (FeCr57) block: 17.5Kg; nickel block: 5Kg; ferromanganese (FeMn75) block: 0.7Kg; vanadium iron (FeV50) block: 4Kg; Granules: 2Kg and iron block: 65.8Kg are mixed and placed in an intermediate frequency furnace to heat to 1000°C-1500°C and kept for 2 hours to fully melt the various components...
Embodiment 2
[0024] The grinding layer welding powder provided by the best embodiment 2 of the present invention contains the following components in weight percentage: chromium: 4-15%; nickel: 3-10%; manganese: 0.2-1%; vanadium: 1-3%; tungsten : 2-10%; silicon: 1-5%; rare earth: 0.5-2%; carbon: 1-5%; the balance is iron and trace impurities.
[0025] The above-mentioned welding powder is composed of ferrochromium (FeCr57) block, nickel block, ferromanganese (FeMn75) block, vanadium iron (FeV50) block, tungsten iron (FeW70) block, metal silicon block, rare earth particles, carbon particles and The iron blocks are mixed and obtained by melting, dusting, drying and sieving.
[0026] Such as figure 1 As shown, ferrochromium (FeCr57) block: 17.5Kg; nickel block: 5Kg; ferromanganese (FeMn75) block: 0.7Kg; vanadium iron (FeV50) block: 4Kg; : 4Kg; Rare earth particles: 1Kg; Carbon particles: 2Kg and iron block: 58.8Kg The mixture is fully mixed and placed in an intermediate frequency furnace to...
Embodiment 3
[0033] The grinding layer welding powder provided by the best embodiment 3 of the present invention contains the following components in weight percentage: chromium: 4-15%; nickel: 3-10%; manganese: 0.2-2%; vanadium: 1-3%; molybdenum : 0.5-3%; tungsten: 2-10%; silicon: 1-5%; rare earth: 0.5-2%; carbon: 1-5%; the balance is iron and trace impurities.
[0034] The above-mentioned welding powder is composed of ferrochromium (FeCr57) block, nickel block, ferromanganese (FeMn75) block, vanadium iron (FeV50) block, molybdenum iron (FeMo60) block, tungsten iron (FeW70) block, metal silicon block in a certain weight ratio , rare earth particles, carbon particles and iron blocks are mixed and obtained by melting, powder spraying, drying and sieving.
[0035] Such as figure 1 As shown, ferrochromium (FeCr57) block: 17.5Kg; nickel block: 5Kg; ferromanganese (FeMn75) block: 0.7Kg; vanadium iron (FeV50) block: 4Kg; (FeW70) block: 7Kg; metal silicon block: 4Kg; rare earth particles: 1Kg; ...
PUM
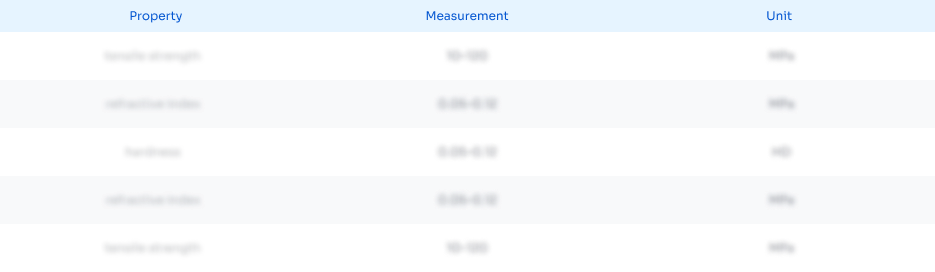
Abstract
Description
Claims
Application Information

- R&D Engineer
- R&D Manager
- IP Professional
- Industry Leading Data Capabilities
- Powerful AI technology
- Patent DNA Extraction
Browse by: Latest US Patents, China's latest patents, Technical Efficacy Thesaurus, Application Domain, Technology Topic.
© 2024 PatSnap. All rights reserved.Legal|Privacy policy|Modern Slavery Act Transparency Statement|Sitemap